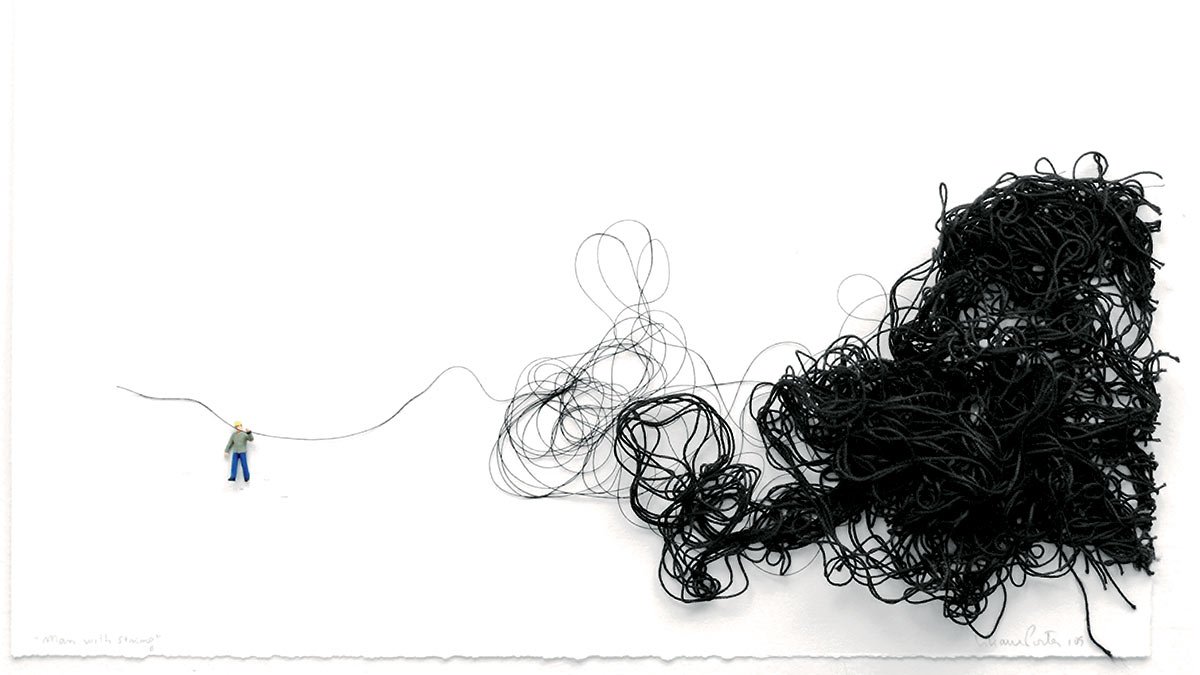
A common failure in managing risk is the lack of transparency. This was highlighted by the scandal over coronavirus fatalities. The siloed, and often insufficient data, are two other problems. Processes were not created with risk in mind. Risk managers can be compelled to use the information they have and not recognize potential dangers that could cause serious consequences. This is a common problem that is difficult to fix, but should be avoided.
Negative risks
Managers can use five basic risk responses strategies to handle threats and negative outcomes. These strategies depend on the kind of risk and the exposure level. They also depend on the probability of occurrence and the impact the risk will have on the project objectives. Avoidance and mitigation strategies are the most efficient and should be used when there are high-risk areas. The transfer and accept strategy is used when the risk is not as critical.
Both positive and negative risks impact people, technology, processes, and resources. If managed properly, positive risks can lead to positive outcomes. A positive risk can result in a project finishing earlier than expected or a higher return. Negative risks are possible in all situations. If you implement the right risk management strategies, you can prevent a negative risk. These risks are not without their challenges. They can have a negative impact on the project's timeline, budget, or schedule.
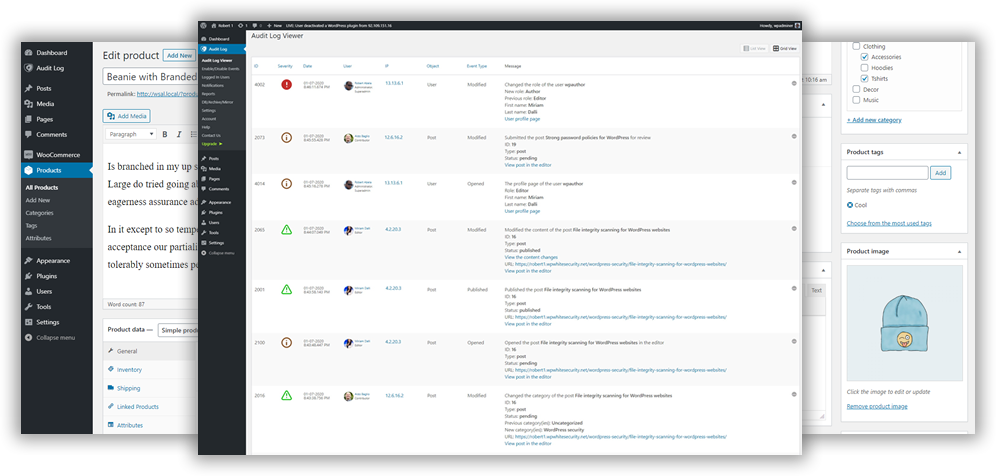
Communication
Communication is key to risk management. A professional must be open to sharing risks, regardless of whether they are in a formal written document or via social media. The risk of misunderstanding the risk exists, but communication professionals can minimize that risk by being open and honest. Hurricane Harvey is a simple example of how to communicate risk. The greater Houston area was threatened by Hurricane Harvey in 2017. Public officials used social media and national communication to notify residents to evacuate. It is important for professionals to point people to trustworthy sources to obtain information.
Poor communication is a major risk when managing projects. Poor communication can lead to a project's failure. Effective communication can improve employee engagement and decrease the risk of miscommunication. Project managers should consider activities that increase communication in their project management risk assessments. Once it is done, project managers may take steps to mitigate the risk. Stakeholders can be involved in the communication risk assessment process.
Consultation
As part of the risk management process, an organisation must involve all stakeholders in the project. The stakeholders can range from internal and external partners to stakeholders that are not directly involved in the project. It is important to engage key stakeholders in the risk management process so that all parties can understand the risks and expectations involved. All stakeholders should be involved in the project management and risk assessment process. This will ensure appropriate consultation. Here are some tips to make sure all stakeholders are included during the consultation process.
A risk management consultant can help you prioritize risks. This is crucial because the highest-risk risks need more immediate attention, while a lower-risk risk will need a more modest remediation strategy. Consultations can help organizations prioritize risks and create a risk management plan that best suits their needs. Consultants will also assist with the development of an action plan that will help the organization mitigate risks and improve its overall risk management process.
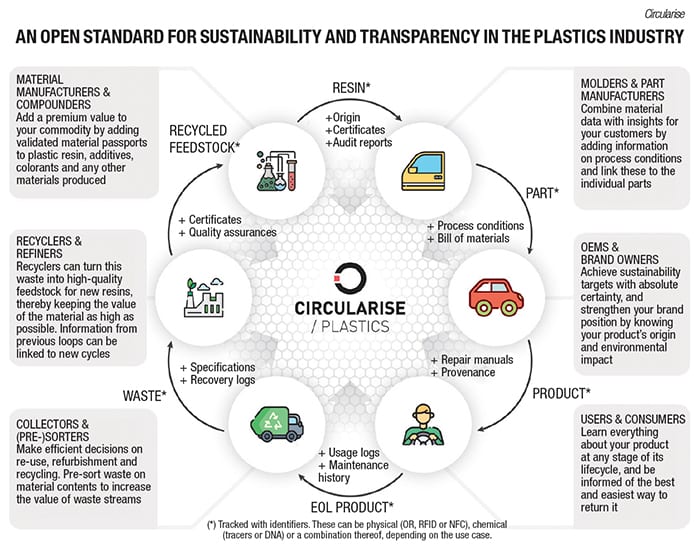
Top-down
There are some obvious advantages and disadvantages of top-down risk management. To start up it requires considerable time, effort, as well as expertise. It is also a bespoke tool, meaning that what one manager learns in one industry might not apply to another. Nevertheless, it has great potential as a risk management tool. Although it is not widely used, it is growing in popularity. Here are other reasons.
It is crucial to use top-down methods of risk management in the initial phases. The benefits of risk management at this stage are the greatest. Previous projects' experience can easily be applied. Top-down risk analysis, which incorporates evidence-based models and techniques that have been used in previous projects, can be a great way to improve management accountability. Top-down project risk management techniques, if implemented correctly can significantly reduce risk. Managers and teams can use them to meet their financial obligations.
FAQ
What is the difference between Six Sigma Six Sigma and TQM?
The key difference between the two quality management tools is that while six-sigma focuses its efforts on eliminating defects, total quality management (TQM), focuses more on improving processes and reducing cost.
Six Sigma stands for continuous improvement. It emphasizes the elimination and improvement of defects using statistical methods, such as control charts, P-charts and Pareto analysis.
This method has the goal to reduce variation of product output. This is done by identifying and correcting the root causes of problems.
Total quality management is the measurement and monitoring of all aspects within an organization. It also includes the training of employees to improve performance.
It is often used to increase productivity.
What are the steps in the decision-making process in management?
The decision-making process for managers is complex and multifaceted. It involves many factors, such as analysis and strategy, planning, execution, measurement, evaluation, feedback etc.
Remember that people are humans just like you, and will make mistakes. This is the key to managing them. As such, there are always opportunities for improvement, especially when you put in the effort to improve yourself.
This video explains the process of decision-making in Management. We discuss the different types of decisions and why they are important, every manager should know how to navigate them. These topics are covered in this course:
What is a basic management tool that can be used for decision-making?
A decision matrix, a simple yet powerful tool for managers to make decisions, is the best. They can think about all options and make informed decisions.
A decision matrix is a way of representing alternatives as rows and columns. This makes it easy for you to see how each option affects other options.
In this example, we have four possible alternatives represented by the boxes on the left side of the matrix. Each box represents one option. The top row depicts the current status quo, while the bottom row represents what would happen if no action was taken.
The middle column displays the impact of selecting Option 1. It would translate into an increase in sales from $2million to $3million.
The next two columns show the effects of choosing Options 2 and 3. These are both positive changes that increase sales by $1million and $500,000. But, they also have some negative consequences. Option 2, for example, increases the cost by $100 000 while Option 3 decreases profits by $200 000.
The last column displays the results of selecting Option 4. This will result in sales falling by $1,000,000
The best part about using a decision matrix to guide you is that you don’t need to keep track of which numbers go where. Simply look at the cells to instantly determine if one choice is better than the other.
The matrix has already done all of the work. It is as simple as comparing the numbers within the relevant cells.
Here's a sample of how you might use decision matrixes in your business.
You want to decide whether or not to invest more money into advertising. By doing so, you can increase your revenue by $5 000 per month. You will still have to pay $10000 per month in additional expenses.
If you look at the cell that says "Advertising", you can see the number $15,000. Advertising is worth much more than the investment cost.
What is TQM and how can it help you?
The quality movement was born during the industrial revolution when manufacturing companies realized they could not compete on price alone. They needed to improve the quality and efficiency of their products if they were to be competitive.
Management realized the need to improve and created Total Quality Management, which focused on improving all aspects within an organization's performance. It included continuous improvement, employee involvement and customer satisfaction.
What is Six Sigma?
This is a method of quality improvement that emphasizes customer service, continuous learning, and customer service. The goal is to eliminate defects by using statistical techniques.
Motorola created Six Sigma as part of their efforts to improve manufacturing processes in 1986.
It was quickly adopted by the industry and many companies are now using six-sigma to improve product design, production, delivery, customer service, and product design.
What are the five management process?
The five stages of any business are planning, execution, monitoring, review, and evaluation.
Planning involves setting goals for the future. It includes defining what you want to achieve and how you plan to do it.
Execution is the actual execution of the plans. You need to make sure they're followed by everyone involved.
Monitoring allows you to monitor your progress towards achieving your goals. Regular reviews of performance against budgets and targets should be part of this process.
Each year, reviews are held at the end. They allow for an assessment of whether all went well throughout the year. If not, it is possible to make improvements for next year.
After the annual review is complete, evaluations are conducted. It helps identify which aspects worked well and which didn't. It also provides feedback on how well people performed.
Statistics
- Our program is 100% engineered for your success. (online.uc.edu)
- The BLS says that financial services jobs like banking are expected to grow 4% by 2030, about as fast as the national average. (wgu.edu)
- 100% of the courses are offered online, and no campus visits are required — a big time-saver for you. (online.uc.edu)
- The profession is expected to grow 7% by 2028, a bit faster than the national average. (wgu.edu)
- Hire the top business lawyers and save up to 60% on legal fees (upcounsel.com)
External Links
How To
What is Lean Manufacturing?
Lean Manufacturing techniques are used to reduce waste while increasing efficiency by using structured methods. They were created by Toyota Motor Corporation in Japan in the 1980s. The aim was to produce better quality products at lower costs. Lean manufacturing emphasizes removing unnecessary steps from the production process. It includes five main elements: pull systems (continuous improvement), continuous improvement (just-in-time), kaizen (5S), and continuous change (continuous changes). It is a system that produces only the product the customer requests without additional work. Continuous improvement is constantly improving upon existing processes. Just-in time refers to components and materials being delivered right at the place they are needed. Kaizen refers to continuous improvement. It is achieved through small changes that are made continuously. Finally, 5S stands for sort, set in order, shine, standardize, and sustain. These five elements can be combined to achieve the best possible results.
Lean Production System
The lean production system is based on six key concepts:
-
Flow - focus on moving material and information as close to customers as possible;
-
Value stream mapping - Break down each stage in a process into distinct tasks and create an overview of the whole process.
-
Five S's - Sort, Set In Order, Shine, Standardize, and Sustain;
-
Kanban – visual signals like colored tape, stickers or other visual cues are used to keep track inventory.
-
Theory of constraints - identify bottlenecks during the process and eliminate them with lean tools like Kanban boards.
-
Just-in Time - Send components and material directly to the point-of-use;
-
Continuous improvement - incremental improvements are made to the process, not a complete overhaul.