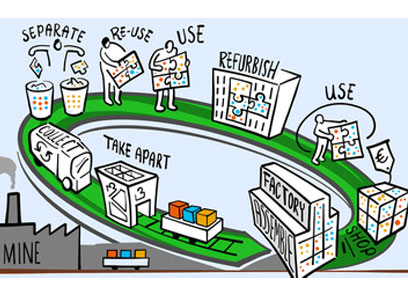
It can increase productivity and help you save time. The average employee receives 120 emails per day, some of which are critical and important, while others are just plain junk. This will allow you to spend less time on irrelevant and unimportant emails and instead respond to the most important. You have a variety of options to manage your email, and improve your productivity.
Two-Minute Rule
The Two-Minute Rule for managing email is a powerful technique for completing quick tasks that can free up a lot of time. Although it won't be a quick fix, it can help speed up the process of getting through your inbox. Its primary purpose is to delete all unimportant messages and clear out your inbox. This can be done by going through each email one by one, either by deleting it or filing them. Or moving them to a tasklist. Sometimes, you don't even have to reply to the email right away.
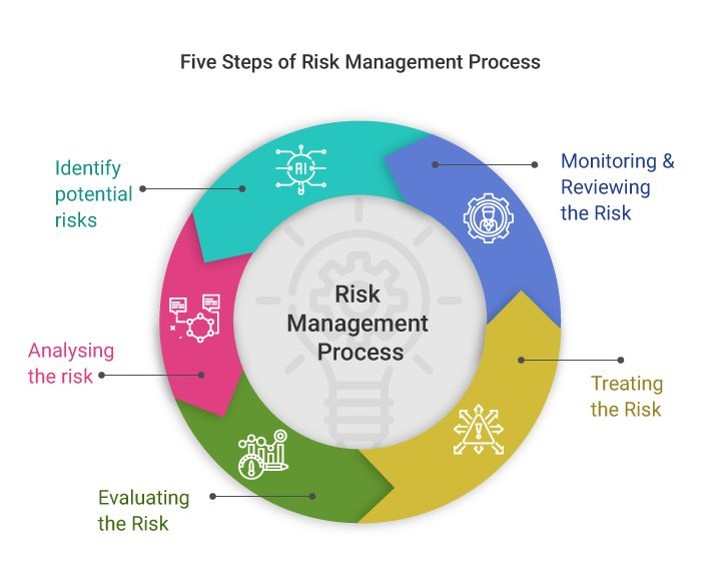
Automated Replies
Automated reply messages can be a great asset in managing email. A reply message can be a great tool in managing email. It will allow you to keep track of the message and let the customer know what you are doing next. By providing customers with transparent information, an auto reply message helps you to maintain a high level of customer engagement. These messages can help you avoid making rash decisions.
Shared Inbox
Managing a shared inbox can be difficult, especially when you're working with multiple people. Multiple shared inboxes can lead to chaos in your workflow. Inefficient email management can also make it easy for you to miss important emails or issues. However, there are best practices to help you manage your shared email inbox. Effective communication is the foundation of a shared inbox.
Filters
Filters are one of the most common methods for categorizing emails. They can be set to do different things, such as delete messages, apply a flag, or move messages to a folder. There are many different types of filters.
Automated deletion
Email management software has an option to automatically delete emails. You can choose whether to delete email messages that are older than 30 calendar days or spam. You can customize these settings by setting them up separately if you wish. Email Studio lets you create multiple purge policies.
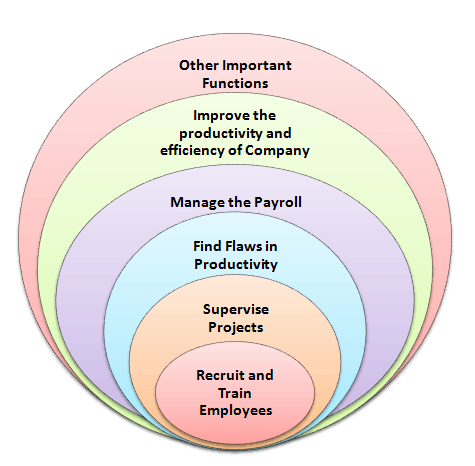
OHIO method
The OHIO method for managing email is a process that aims to clear the inbox and increase productivity. It is a straightforward decision-making process that handles incoming emails and turns them into actionable items. Emails that don't require immediate action may be archived or deleted.
FAQ
What is a simple management tool that aids in decision-making and decision making?
A decision matrix is an easy but powerful tool to aid managers in making informed decisions. It helps them think systematically about all the options available to them.
A decision matrix is a way of representing alternatives as rows and columns. This allows one to see how each alternative impacts other options.
The boxes on the left hand side of this matrix represent four possible choices. Each box represents one option. The top row shows the status quo (the current situation), and the bottom row shows what would happen if nothing was done at all.
The middle column displays the impact of selecting Option 1. It would increase sales by $2 million to 3 million in this instance.
These are the results of selecting Options 2 or 3. These are positive changes - they increase sales by $1 million and $500 thousand respectively. They also have negative consequences. Option 2, for example, increases the cost by $100 000 while Option 3 decreases profits by $200 000.
Finally, the last column shows the results of choosing Option 4. This results in a decrease of sales by $1,000,000
A decision matrix has the advantage that you don’t have to remember where numbers belong. You just look at the cells and know immediately whether any given a choice is better than another.
The matrix has already done all of the work. It is as simple a matter of comparing all the numbers in each cell.
Here is an example how you might use the decision matrix in your company.
You need to decide whether to invest in advertising. If you do, you'll be able to increase your revenue by $5 thousand per month. You will still have to pay $10000 per month in additional expenses.
By looking at the cell just below "Advertising", the net result can be calculated as $15 thousand. Advertising is a worthwhile investment because it has a higher return than the costs.
What is the difference between Six Sigma Six Sigma and TQM?
The main difference in these two quality management tools lies in the fact that six sigma is focused on eliminating defects and total quality management (TQM), emphasizes improving processes and reducing costs.
Six Sigma is a methodology for continuous improvement. It emphasizes the elimination or minimization of defects through statistical methods such control charts and p charts.
This method has the goal to reduce variation of product output. This is achieved by identifying and addressing the root causes of problems.
Total Quality Management involves monitoring and measuring every aspect of the organization. Training employees is also part of total quality management.
It is used to increase productivity.
How do we build a culture that is successful in our company?
A successful company culture is one that makes people feel valued and respected.
It's founded on three principal principles:
-
Everybody has something of value to share
-
People are treated fairly
-
Individuals and groups can have mutual respect
These values can be seen in the behavior of people. For example, they will treat others with courtesy and consideration.
They will listen respectfully to the opinions of others.
They can also be a source of inspiration for others.
A company culture encourages collaboration and communication.
People are free to speak out without fear of reprisal.
They understand that mistakes can be forgiven as long as they're dealt with honestly.
Finally, the company culture promotes honesty and integrity.
Everyone knows that they must always tell truth.
Everyone understands there are rules that they must follow.
People don't expect special treatment or favors.
Statistics
- This field is expected to grow about 7% by 2028, a bit faster than the national average for job growth. (wgu.edu)
- The profession is expected to grow 7% by 2028, a bit faster than the national average. (wgu.edu)
- As of 2020, personal bankers or tellers make an average of $32,620 per year, according to the BLS. (wgu.edu)
- Hire the top business lawyers and save up to 60% on legal fees (upcounsel.com)
- Your choice in Step 5 may very likely be the same or similar to the alternative you placed at the top of your list at the end of Step 4. (umassd.edu)
External Links
How To
What is Lean Manufacturing?
Lean Manufacturing processes are used to reduce waste and improve efficiency through structured methods. They were developed by Toyota Motor Corporation in Japan during the 1980s. The aim was to produce better quality products at lower costs. Lean manufacturing eliminates unnecessary steps and activities from a production process. It is made up of five elements: continuous improvement, continuous improvement, just in-time, continuous change, and 5S. Pull systems involve producing only what the customer wants without any extra work. Continuous improvement refers to continuously improving existing processes. Just-in-time is when components and other materials are delivered at their destination in a timely manner. Kaizen means continuous improvement. Kaizen involves making small changes and improving continuously. Last but not least, 5S is for sort. These five elements can be combined to achieve the best possible results.
Lean Production System
Six key concepts underlie the lean production system.
-
Flow - The focus is on moving information and material as close as possible to customers.
-
Value stream mapping is the ability to divide a process into smaller tasks, and then create a flowchart that shows the entire process.
-
Five S's: Sort, Shine Standardize, Sustain, Set In Order, Shine and Shine
-
Kanban: Use visual signals such stickers, colored tape, or any other visual cues, to keep track your inventory.
-
Theory of constraints - identify bottlenecks in the process and eliminate them using lean tools like kanban boards;
-
Just-in time - Get components and materials delivered right at the point of usage;
-
Continuous improvement: Make incremental improvements to the process instead of overhauling it completely.