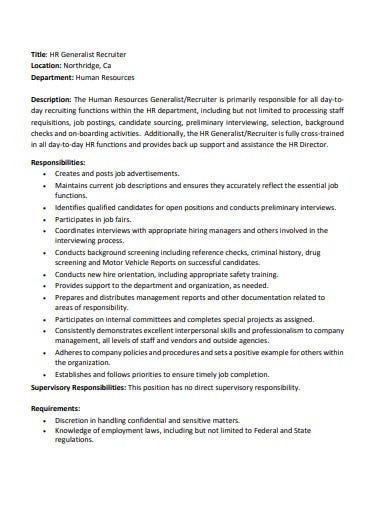
Demand planning is a process that assists businesses in managing their supply chains and sales. This is done to reduce costs and improve service levels. This process includes three major components: sales forecasting and inventory management. It can help businesses improve their planning and reduce inventory.
Demand planning combines sales forecasting with inventory management and supply chains management.
Supply chain management's most important component is demand planning. This involves the systematic study and analysis of customer demand as well as inventory levels. This requires the assessment of many factors including seasonal shifts, economic conditions and environmental changes. When done right, demand planning allows retailers to stay competitive and capitalize on sales opportunities. In addition, demand planning helps retailers better manage their resources and adjust their plans in real time. For accurate demand forecasts to be made, there must be a lot of data. Therefore, retailers need the right infrastructure and tools to collect this data.
Developing a demand plan involves collecting data from all departments, monitoring market changes, and involving the appropriate stakeholders. In order for success, demand management must be integrated with supply chains management, inventory management, or other processes.
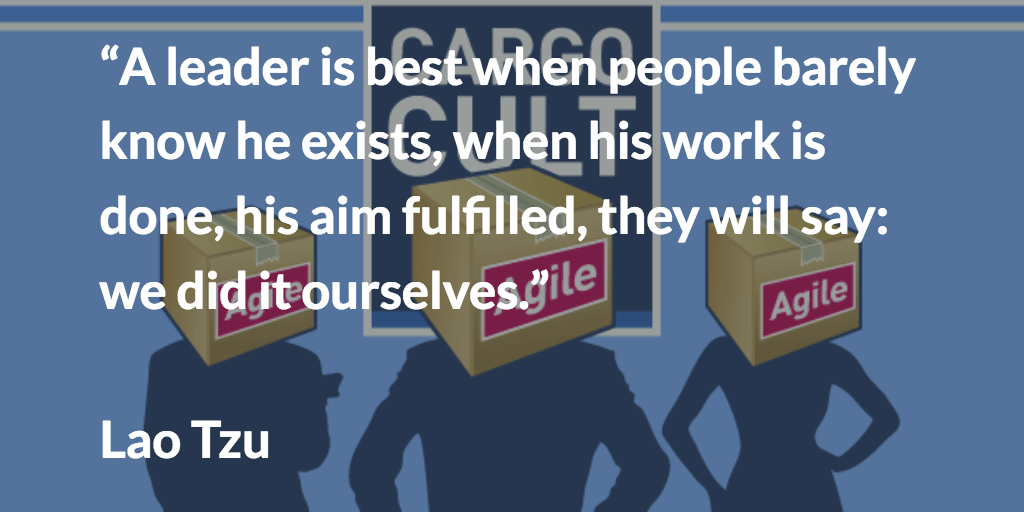
It helps companies plan operations better
Businesses need to plan their demand in order to maintain a balance between stock levels and customer demand. It requires coordination from all departments. Unnecessary inventory could lead to loss of revenue and higher inventory carrying expenses. It increases the possibility of stockouts and low-value inventory. Poor demand planning can cause supply chain disruptions, stockouts and costly scrambles to find raw materials. This can ultimately lead to unhappy customers.
Companies must collect and analyze past sales data, seasonality and customer trends in order to do accurate demand planning. Combined with inventory management, this information can be used to better predict future demand and make decisions on purchase orders.
It reduces costs
The best way to cut costs is demand planning. Not only can it cut production costs, but it will also save money on warehousing. It also helps companies keep their inventory levels more manageable by having fewer items on hand. How to implement demand planning in your company. Remember to communicate well.
A good demand plan will allow you to balance customer demand and inventory. This requires coordination throughout your organization. Lack of planning can lead to excess inventory in your company, which could result in a loss of working capital, as well as increased inventory carrying costs. This could lead to obsolete products or inventory with low value. Poor planning can also result in disruptions to the supply chain, stockouts, and costly scrambles just to get raw materials. This can lead to customer dissatisfaction and even cause delays.
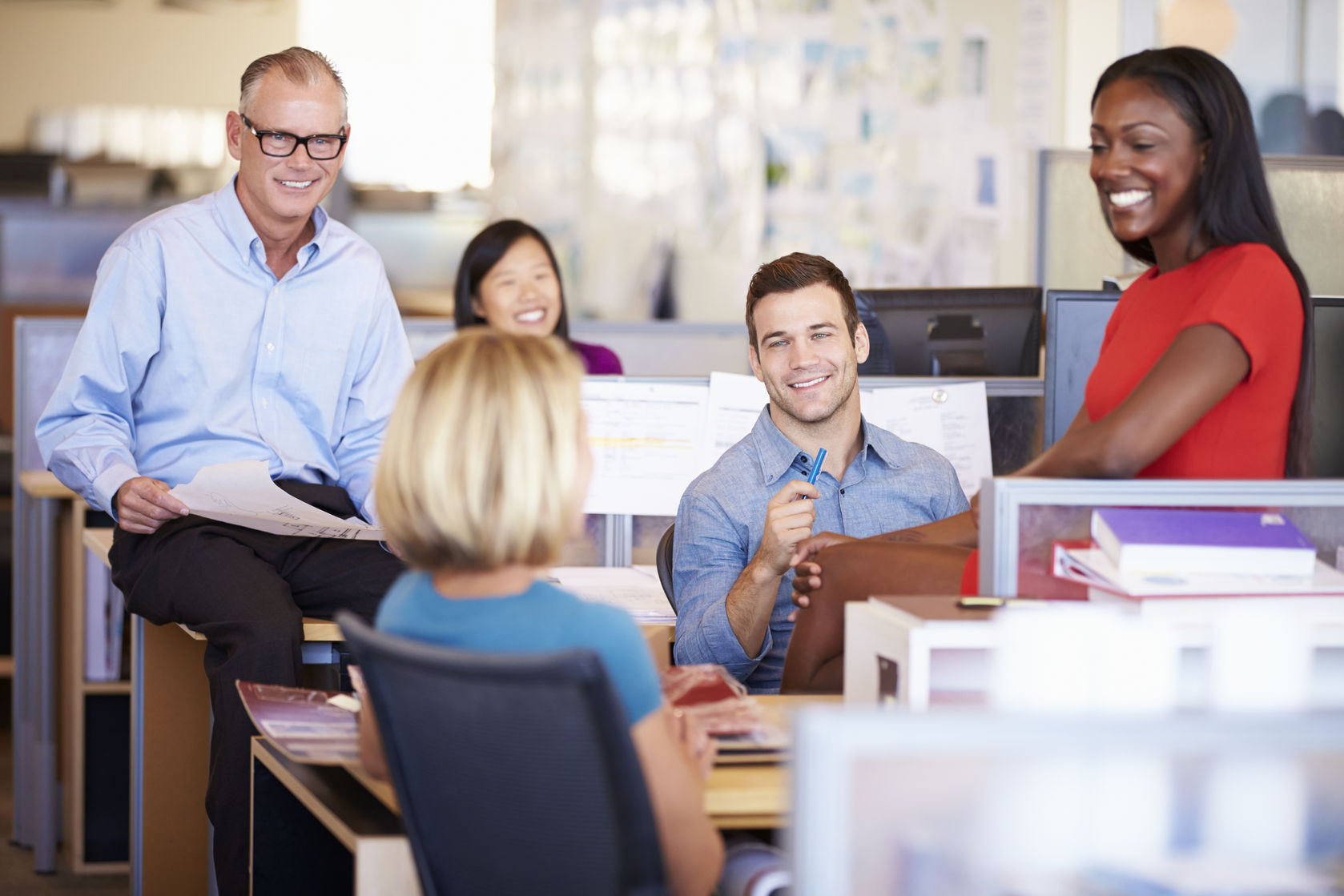
It enhances service levels
A key step in helping retailers meet customer demands is planning demand. Demand planning is a process that helps retailers plan inventory, purchase, and storage. It also indicates how much stock is needed for a particular product and helps refine forecasting processes. Once a business has established a workable demand planning process, it can easily be used to guide sales and operations planning.
FAQ
What are the five management steps?
The five stages of a business include planning, execution (monitoring), review, evaluation, and review.
Setting goals for the future is part of planning. Planning includes setting goals for the future.
Execution is when you actually execute the plans. You need to make sure they're followed by everyone involved.
Monitoring is a way to track progress towards your objectives. Regular reviews should be done of your performance against targets or budgets.
Each year, reviews are held at the end. They allow for an assessment of whether all went well throughout the year. If not, changes may be made to improve the performance next time around.
Evaluation takes place after the annual review. It helps identify which aspects worked well and which didn't. It also provides feedback on how well people performed.
What are the 3 main management styles?
These are the three most common management styles: participative (authoritarian), laissez-faire (leavez-faire), and authoritarian. Each style has its advantages and disadvantages. Which style do you prefer? Why?
Authoritarian - The leader sets the direction and expects everyone to comply with it. This style works best if the organization is large and stable.
Laissez faire - Each individual can decide for himself/herself. This style is best when the organization has a small but dynamic group.
Participative - The leader listens to ideas and suggestions from everyone. This style is most effective in smaller organizations, where everyone feels valued.
What is Six Sigma?
It's a method for quality improvement that focuses on customer service as well as continuous learning. The goal is to eliminate defects by using statistical techniques.
Six Sigma was developed at Motorola in 1986 as part of its efforts to improve manufacturing processes.
It was quickly adopted by the industry and many companies are now using six-sigma to improve product design, production, delivery, customer service, and product design.
Statistics
- The profession is expected to grow 7% by 2028, a bit faster than the national average. (wgu.edu)
- This field is expected to grow about 7% by 2028, a bit faster than the national average for job growth. (wgu.edu)
- 100% of the courses are offered online, and no campus visits are required — a big time-saver for you. (online.uc.edu)
- Our program is 100% engineered for your success. (online.uc.edu)
- As of 2020, personal bankers or tellers make an average of $32,620 per year, according to the BLS. (wgu.edu)
External Links
How To
What is Lean Manufacturing?
Lean Manufacturing processes are used to reduce waste and improve efficiency through structured methods. They were developed by Toyota Motor Corporation in Japan during the 1980s. The aim was to produce better quality products at lower costs. Lean manufacturing focuses on eliminating unnecessary steps and activities from the production process. It consists of five basic elements: pull systems, continuous improvement, just-in-time, kaizen (continuous change), and 5S. Pull systems involve producing only what the customer wants without any extra work. Continuous improvement is the continuous improvement of existing processes. Just-in–time refers when components or materials are delivered immediately to their intended destination. Kaizen means continuous improvement. Kaizen involves making small changes and improving continuously. Last but not least, 5S is for sort. These five elements are used together to ensure the best possible results.
Lean Production System
Six key concepts are the basis of lean production:
-
Flow is about moving material and information as near as customers can.
-
Value stream mapping: This is a way to break down each stage into separate tasks and create a flowchart for the entire process.
-
Five S’s - Sorted, In Order. Shine. Standardize. And Sustain.
-
Kanban - visual cues such as stickers or colored tape can be used to track inventory.
-
Theory of Constraints - Identify bottlenecks in the process, and eliminate them using lean tools such kanban boards.
-
Just-in Time - Send components and material directly to the point-of-use;
-
Continuous improvement is making incremental improvements to your process, rather than trying to overhaul it all at once.