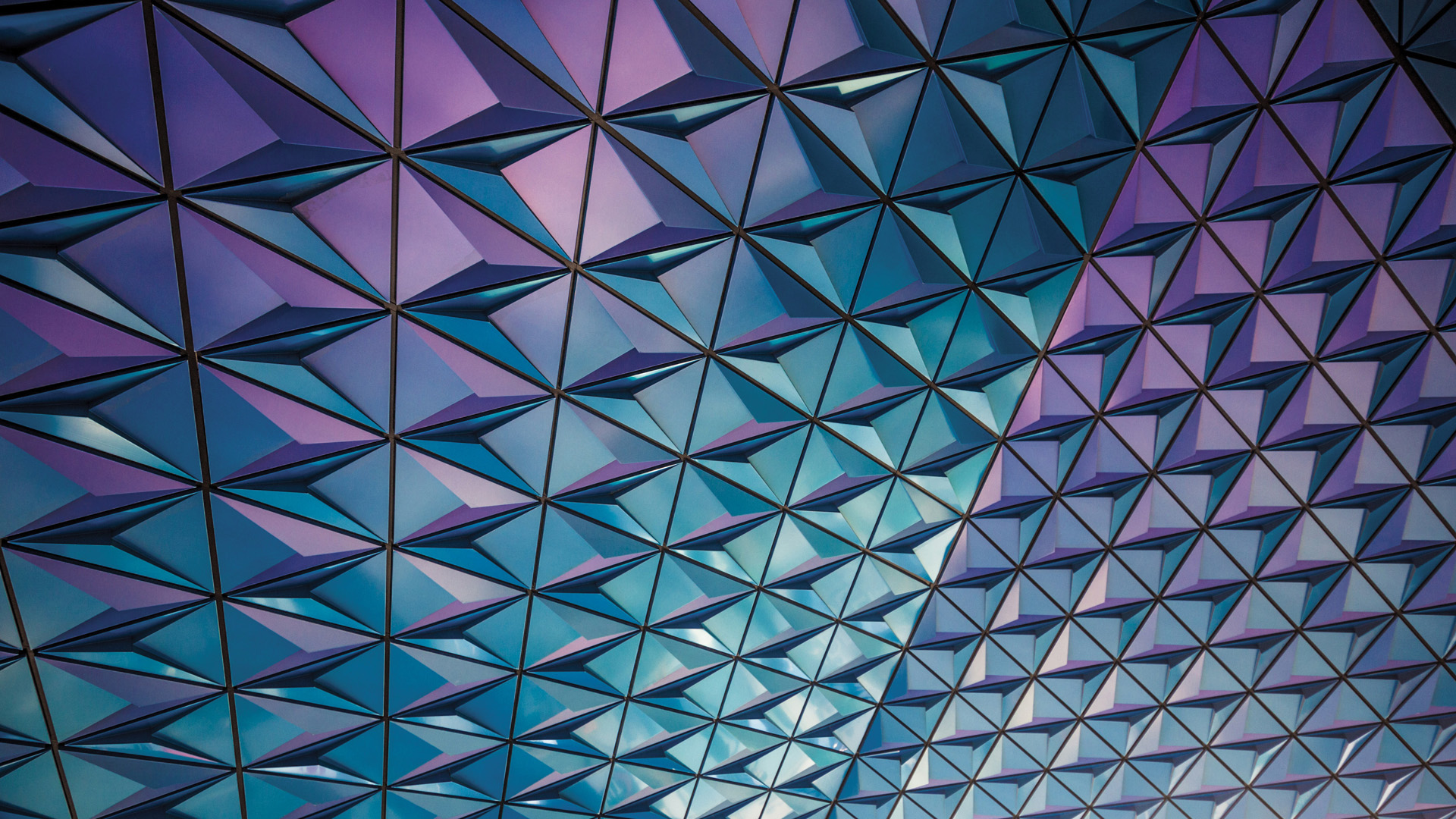
Integrated supply chain management (ISM) is a holistic approach for managing a business. It involves the "cradle management" of a business. This management approach involves asymmetrical relationships between buyers or sellers. Its goal is to improve quality and reduce costs. It also involves end-to-end visibility. This is an important part of fully integrated supply chains. Not all companies will be interested in this approach.
Integrated supply chain management is a "cradle-to-grave" approach
Integrated supply chain management (ISCM) is a holistic concept that covers all aspects in the product life cycle. This includes raw materials and consumer products. It includes forward and reverse logistics, information flows and cash flows. This is typically between producers and distributors and retailers. The ultimate goal should be to minimize waste and maximize benefits to the end user. Supply chain managers have to learn how to maximize outside resources and recycle materials after their useful life spans.

It is characterized as adversarial relationships among buyers and sellers
The integration of supply chain management requires reducing the number transactions and maximising the performance. It requires disciplined management skills, technologies and processes. Additionally, it requires a focus on key capabilities. The ultimate goal of the project is to achieve higher profitability while reducing risk for everyone. In today's global economic climate, this is not always easy to achieve. However, with some common practices, integrating supply chain management can be an effective and cost-efficient strategy.
It lowers costs
Integrated supply chain management can reduce costs for your business in many ways. You must ensure your suppliers are meeting your specifications and their prices meet your expectations. Suppliers should have a good track record and be able deliver the goods in a timely manner. This is especially important when you deal with perishable commodities. You can increase the efficiency of your business by implementing more efficient supply chain management practices.
It improves quality
Integrated supply chain management is a single, centralized view that shows all of an organization's supply operations. The supply chain can be easily updated from this central view without investing in hardware and software. This makes it agile and scalable. Organizations can make better business decisions, work with vendors, and leverage real-time data to improve their planning. It's a win/win situation for everyone involved. These are just some of the benefits you get from integrating your supply chain.
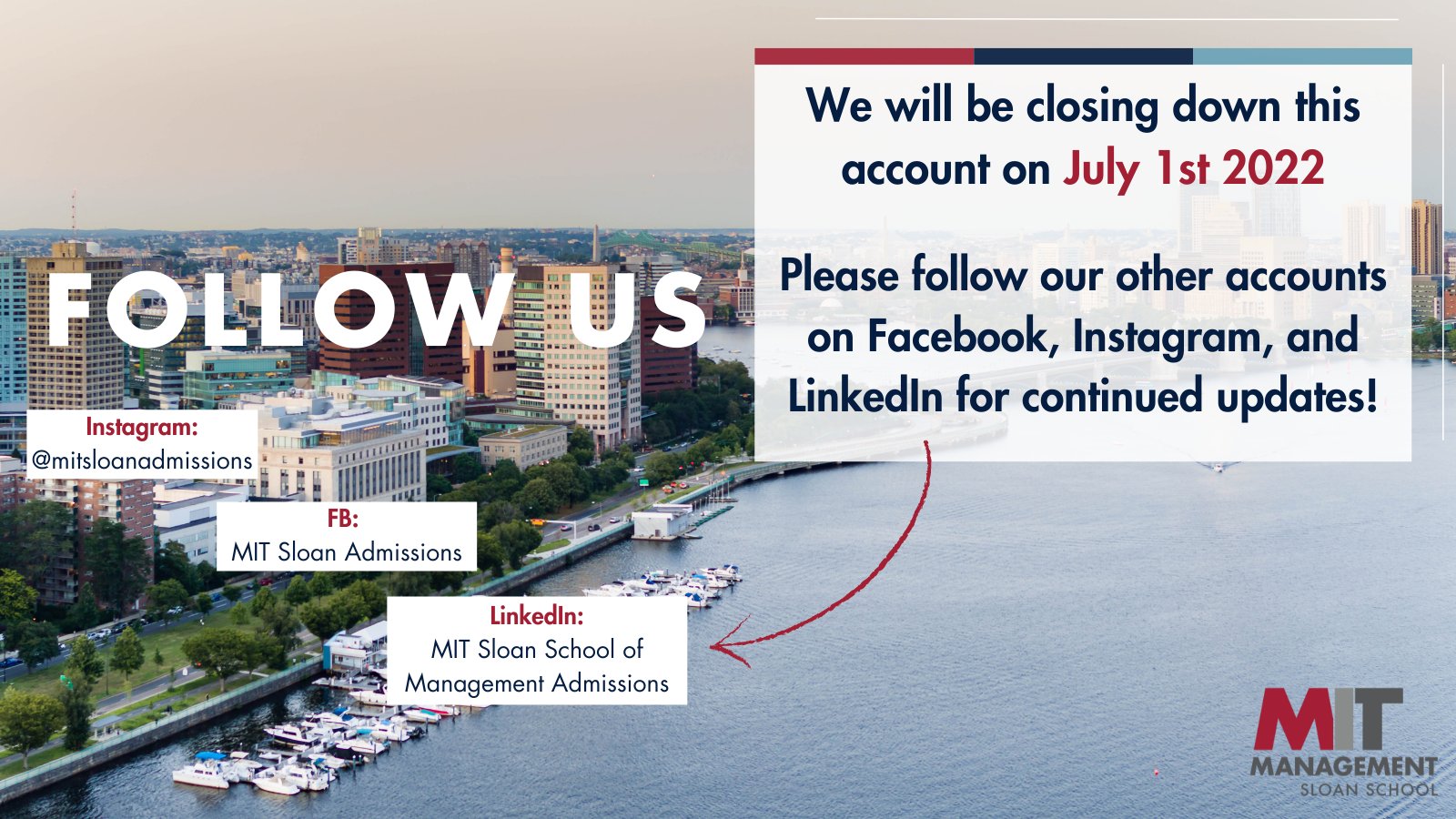
It allows for quick product design, manufacturing, and assembly
With the advent of integrated supply chain management, manufacturers can now design and produce full products in less time than it used to take. This trend can reduce material wastage and warehouse costs. On-demand production also offers better customer service. The only downside is the steep learning curve. However, you can create products in as little time as one day by using new materials or hardware. It can also improve product quality.
FAQ
Why is it so hard to make smart business decisions?
Complex systems with many moving parts are the hallmark of businesses. Their leaders must manage multiple priorities, as well as dealing with uncertainty.
It is important to understand the effects of these factors on the system in order to make informed decisions.
This requires you to think about the purpose and function of each component. Then, you need to think about how these pieces interact with one another.
It is also worth asking yourself if you have any unspoken assumptions about how you have been doing things. You might consider revisiting them if they are not.
Asking for assistance from someone else is a good idea if you are still having trouble. They may see things differently from you and have insights that could help you find a solution.
What are the four major functions of Management?
Management is responsible for planning, organizing, directing, and controlling people and resources. Management also involves setting goals and developing policies.
Management helps an organization achieve its objectives by providing direction, coordination, control, leadership, motivation, supervision, training, and evaluation.
These are the four major functions of management:
Planning - Planning is about determining what must be done.
Organizing is the act of deciding how things should go.
Directing - Directing is when you get people to do what you ask.
Controlling - Controlling means ensuring that people carry out tasks according to plan.
What are the five management methods?
The five stages of a business include planning, execution (monitoring), review, evaluation, and review.
Setting goals for the future is part of planning. It involves setting goals and making plans.
Execution takes place when you actually implement the plans. They must be followed by all parties.
Monitoring is checking on progress towards achieving your objectives. Regular reviews of performance against budgets and targets should be part of this process.
At the end of every year, reviews take place. They are a chance to see if everything went smoothly during the year. If not then, you can make changes to improve your performance next year.
Following the annual review, evaluation is done. It helps identify which aspects worked well and which didn't. It also provides feedback on how well people performed.
What is Six Sigma?
This is a method of quality improvement that emphasizes customer service, continuous learning, and customer service. The goal is to eliminate defects by using statistical techniques.
Motorola created Six Sigma as part of their efforts to improve manufacturing processes in 1986.
The idea spread quickly throughout the industry, and today, many organizations are using six sigma methods to improve product design, production, delivery, and customer service.
How do you define Six Sigma?
People who have worked with statistics and operations research will usually be familiar with the concepts behind six sigma. It can be used by anyone in any business aspect.
Because it requires a high level of commitment, only those with strong leadership skills will make an effort necessary to implement it successfully.
Statistics
- 100% of the courses are offered online, and no campus visits are required — a big time-saver for you. (online.uc.edu)
- The average salary for financial advisors in 2021 is around $60,000 per year, with the top 10% of the profession making more than $111,000 per year. (wgu.edu)
- As of 2020, personal bankers or tellers make an average of $32,620 per year, according to the BLS. (wgu.edu)
- The BLS says that financial services jobs like banking are expected to grow 4% by 2030, about as fast as the national average. (wgu.edu)
- This field is expected to grow about 7% by 2028, a bit faster than the national average for job growth. (wgu.edu)
External Links
How To
How do I do the Kaizen Method?
Kaizen means continuous improvement. Kaizen is a Japanese concept that encourages constant improvement by small incremental changes. It's a process where people work together to improve their processes continuously.
Kaizen, a Lean Manufacturing method, is one of its most powerful. This concept requires employees to identify and solve problems during manufacturing before they become major issues. This way, the quality of products increases, and the cost decreases.
Kaizen is about making everyone aware of the world around them. To prevent problems from happening, any problem should be addressed immediately. If someone spots a problem while at work, they should immediately report it to their manager.
When doing kaizen, there are some principles we must follow. We always start from the end product and move toward the beginning. If we want to improve our factory for example, we start by fixing the machines that make the final product. Next, we fix the machines which produce components. We then fix the workers that work with those machines.
This is why it's called "kaizen" because it works step-by-step to improve everything. We finish fixing the factory and then go back to the beginning. This continues until we achieve perfection.
It is important to understand how to measure the effectiveness and implementation of kaizen in your company. There are several ways to determine whether kaizen is working well. One of these ways is to check the number of defects found on the finished products. Another way is to see how much productivity has increased since implementing kaizen.
A good way to determine whether kaizen has been implemented is to ask why. Did you do it because it was legal or to save money? Did you really think that it would help you achieve success?
If you answered yes to any one of these questions, congratulations! You're ready to start kaizen.