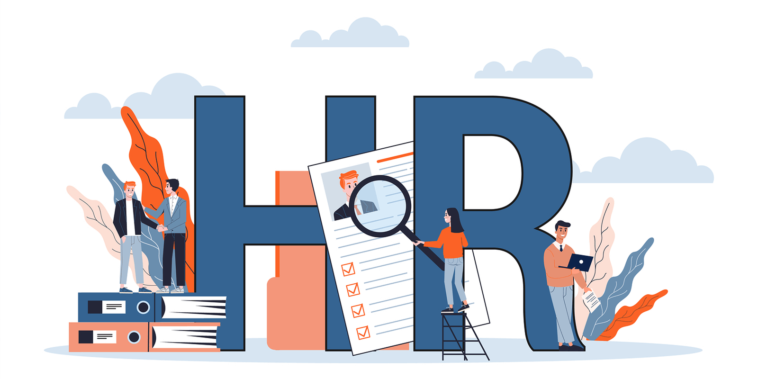
Corporate transformations are not a success story. While consultants and scholars have improved our understanding of this phenomenon, the latest studies indicate that three-quarters of change efforts fail to deliver the anticipated benefits. This is why these transformations often fail to deliver the expected benefits. Here are some ways to improve change management:
Lessons learned from ASDA's Driving Test
ASDA's case study provides interesting insight into the role of experimentation, evolution and change management. ASDA established an experimental store to test its potential and expanded it later to three more. All three were declared risk-free. The driving force behind this case study changed ASDA’s retail proposition, organizational structures, and management team. They also encouraged store managers to experiment in product layouts, employee roles, and product ranges. The result was a remarkable rate of success.
ASDA's executive were awarded stock options that were tied to company value. This helped to attract and retain key executives, and drove rapid company transformation. The company's stock ownership plan paid variable compensation to employees based both on store records as well as corporate performance. Despite all the challenges that came up, the culture of trust and openness created was a success immediately.
How to improve your change management
HR professionals need to ensure the change is implemented smoothly and effectively, in addition to leading it. They must plan the implementation phases and identify key roles. They must listen to employees and adjust plans as required. Human resources professionals can assist with change management by using education and technology. The following are some ways to improve change management HR in your company. Use them to improve your change management process.
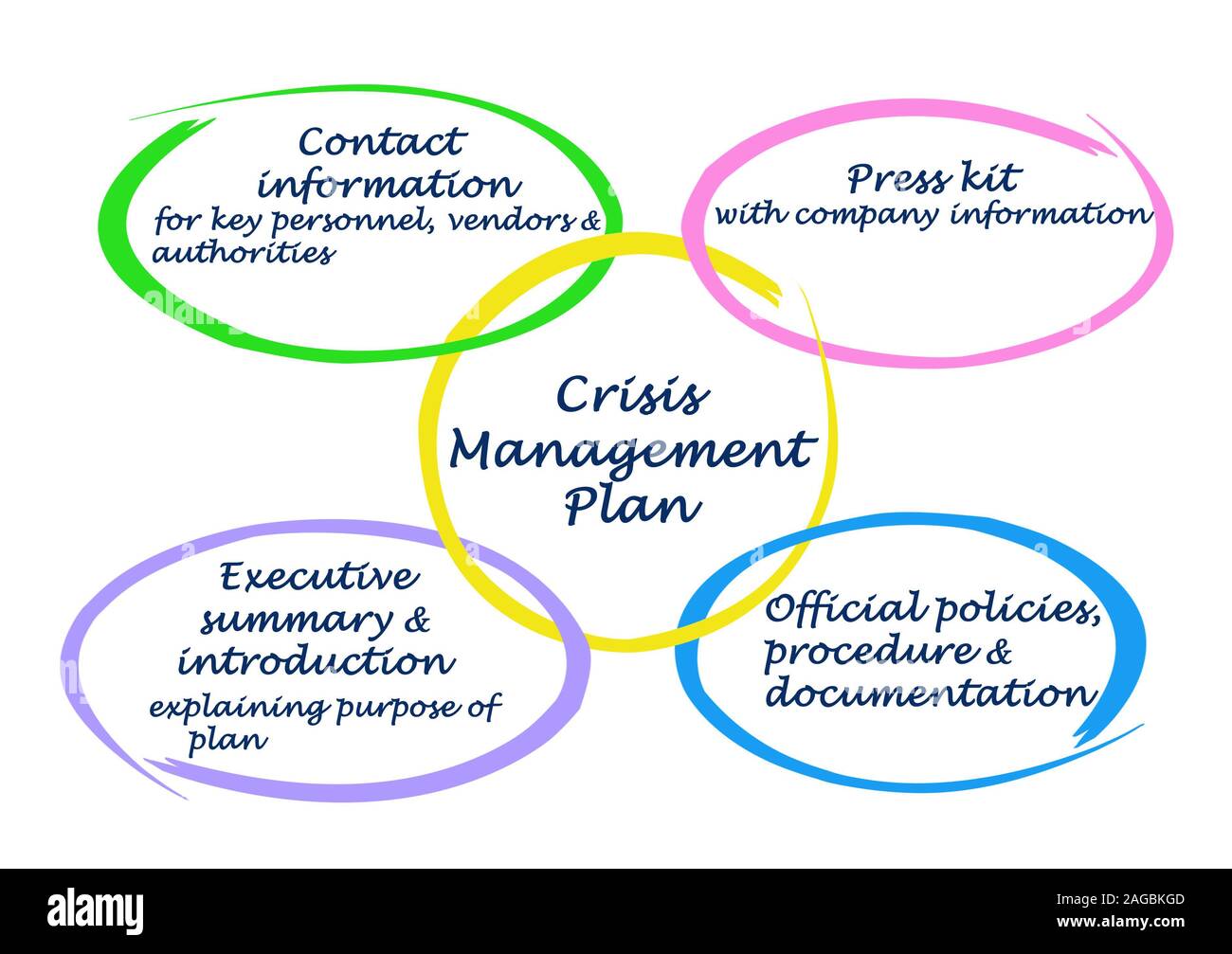
Identify those employees who are affected. Employees want the opportunity to contribute to the process. This is why a change channel should exist to collect employee feedback. To help managers make informed decisions about the change, invest in employee engagement and training. Employees will also be benefited from the training and information provided to them by managers about the change. Involve employees in the process, including managers, to create a positive culture. Recognize their contribution and encourage them to do so.
FAQ
What are the 5 management processes?
Planning, execution, monitoring and review are the five stages of any business.
Planning is about setting goals for your future. This includes setting goals for the future and defining what you want.
Execution happens when you actually do the plan. These plans must be adhered to by everyone.
Monitoring is a way to track progress towards your objectives. Regular reviews of performance against targets, budgets, and other goals should be part.
Each year, reviews are held at the end. These reviews allow you to evaluate whether the year was successful. If not, then it may be possible to make adjustments in order to improve performance next time.
After each year's review, evaluation occurs. It helps to identify what went well and what didn’t. It also gives feedback on how well people did.
What role does a manager play in a company?
There are many roles that a manager can play in different industries.
The manager oversees the day-to-day activities of a company.
He/she ensures that the company meets its financial obligations and produces goods or services that customers want.
He/she makes sure that employees adhere to the rules and regulations as well as quality standards.
He/she oversees marketing campaigns and plans new products.
What is TQM?
The industrial revolution saw the realization that prices alone were not sufficient to sustain manufacturing companies. This led to the birth of quality. They needed to improve the quality and efficiency of their products if they were to be competitive.
Management developed Total Quality Management to address the need for improvement. It focused on all aspects of an organisation's performance. It included continuous improvement, employee involvement and customer satisfaction.
Statistics
- Our program is 100% engineered for your success. (online.uc.edu)
- Hire the top business lawyers and save up to 60% on legal fees (upcounsel.com)
- The BLS says that financial services jobs like banking are expected to grow 4% by 2030, about as fast as the national average. (wgu.edu)
- This field is expected to grow about 7% by 2028, a bit faster than the national average for job growth. (wgu.edu)
- UpCounsel accepts only the top 5 percent of lawyers on its site. (upcounsel.com)
External Links
How To
What is Lean Manufacturing?
Lean Manufacturing uses structured methods to reduce waste, increase efficiency and reduce waste. These processes were created by Toyota Motor Corporation, Japan in the 1980s. The main goal was to produce products at lower costs while maintaining quality. Lean manufacturing eliminates unnecessary steps and activities from a production process. It is made up of five elements: continuous improvement, continuous improvement, just in-time, continuous change, and 5S. Pull systems allow customers to get exactly what they want without having to do extra work. Continuous improvement refers to continuously improving existing processes. Just-in-time refers to when components and materials are delivered directly to the point where they are needed. Kaizen means continuous improvement. Kaizen involves making small changes and improving continuously. The 5S acronym stands for sort in order, shine standardize and maintain. These five elements are used together to ensure the best possible results.
Lean Production System
Six key concepts underlie the lean production system.
-
Flow - focus on moving material and information as close to customers as possible;
-
Value stream mapping - Break down each stage in a process into distinct tasks and create an overview of the whole process.
-
Five S’s - Sorted, In Order. Shine. Standardize. And Sustain.
-
Kanban - visual cues such as stickers or colored tape can be used to track inventory.
-
Theory of constraints - identify bottlenecks during the process and eliminate them with lean tools like Kanban boards.
-
Just-in time - Get components and materials delivered right at the point of usage;
-
Continuous improvement - make incremental improvements to the process rather than overhauling it all at once.