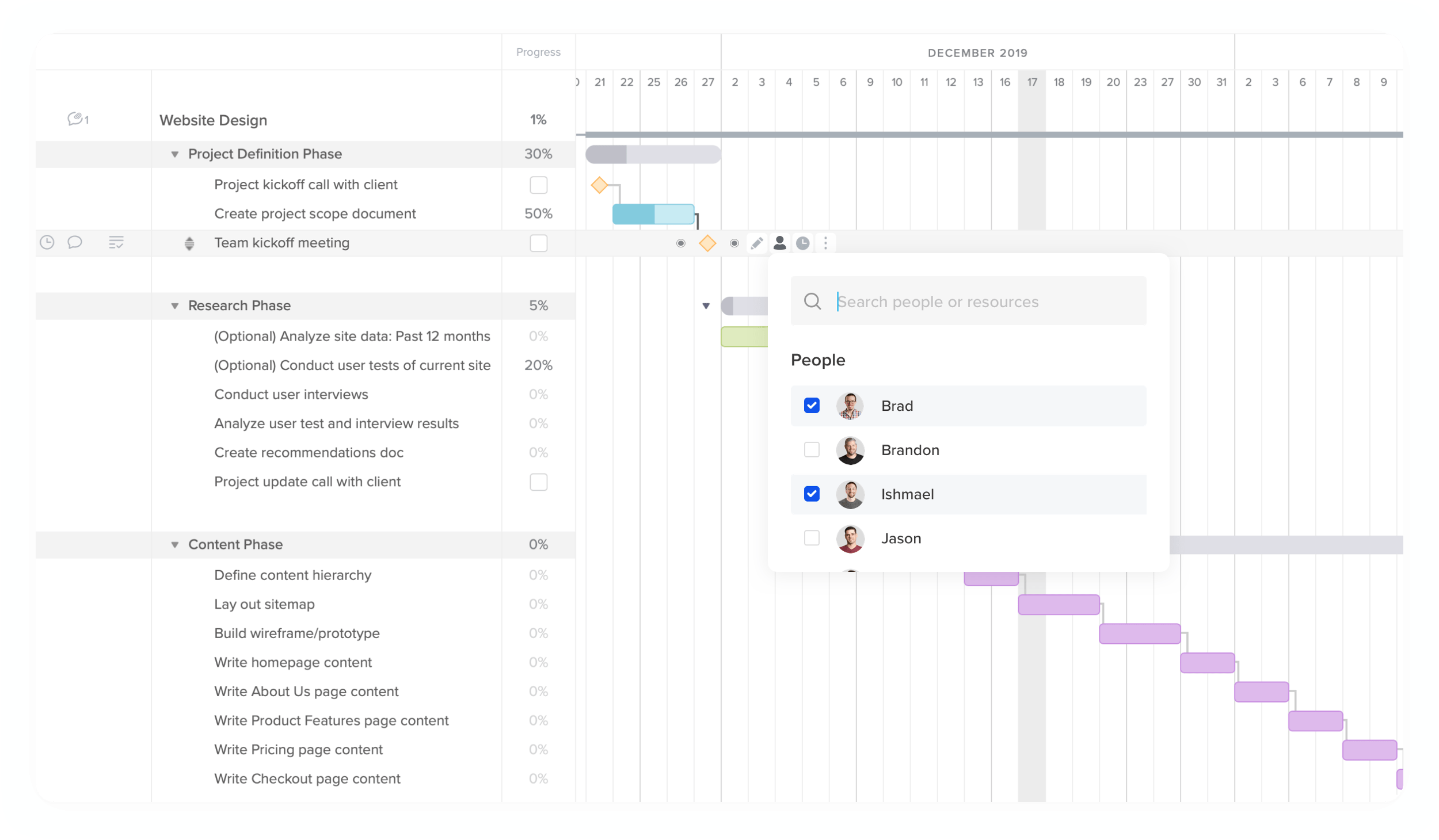
Any project, small or large is incomplete without risk management plans. Your risk management plan will help you to reduce risks associated with your project. Here are some tips for creating a risk management plan. Before you begin writing, you need to assess all of the risks. This will help you choose risks with the highest impact and likelihood, and create a plan to mitigate them. So that you can put it into action as soon as possible, make sure your plan stays current and complete.
Create a risk management plan
Risk management plans are a powerful tool to manage risks and increase your chances of success. This plan helps to reduce or eliminate any negative risks and makes it easier for your team to be prepared. You can ensure that your project achieves its objectives by having a clear risk management plan. If it isn't done correctly, it could pose a risk to your project. Therefore, it's essential to have a risk management plan that is simple, concise, and easy to understand.
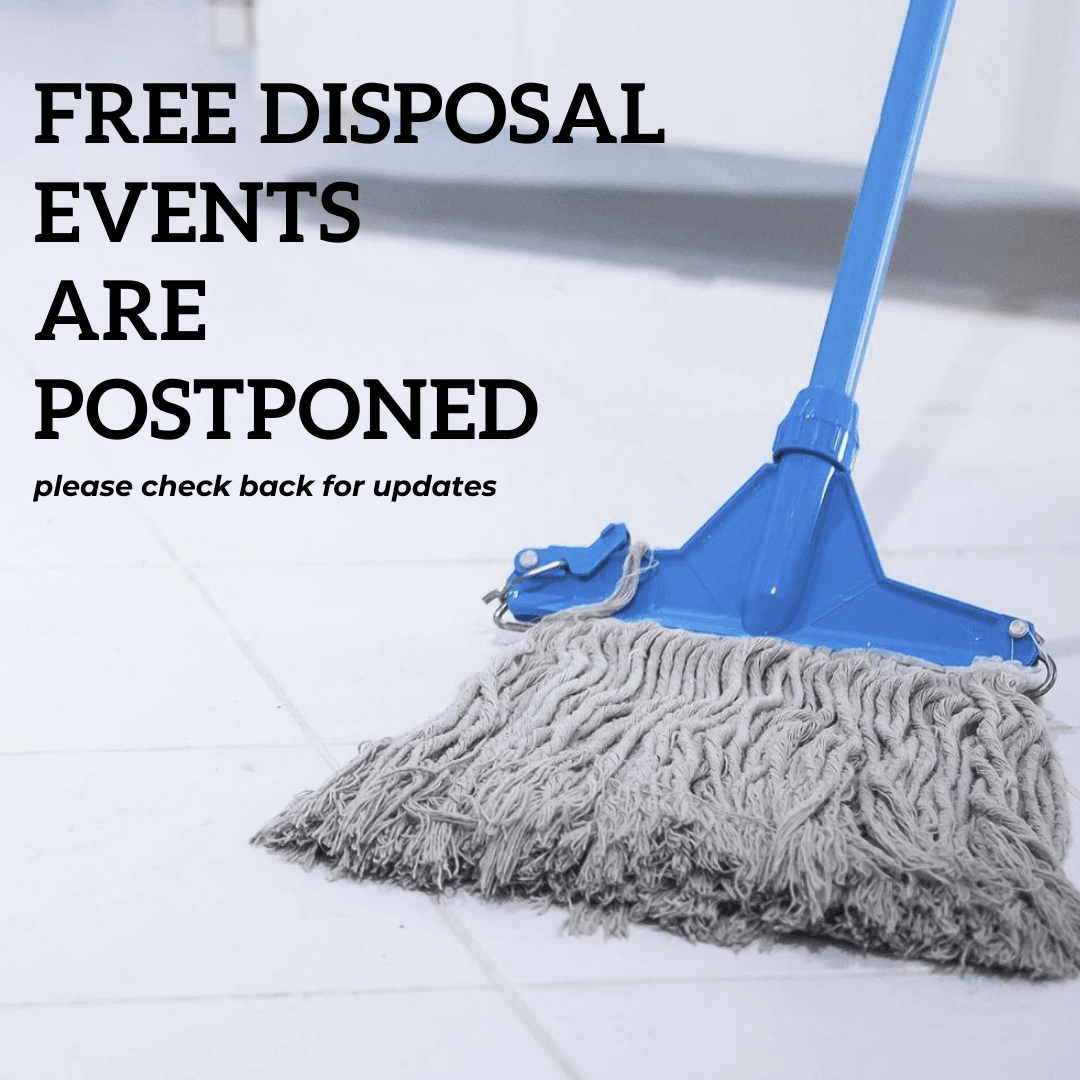
Steps to creating a plan
First, identify the risks and potential solutions. This should be done together and include input from team members as well as subject matter experts. Next is to identify and prioritize risks, and to determine the resources that are needed to reduce or prevent them. It is important to include a communication plan in your risk management plan. This will help you keep the team on track. It should also include a list with all possible solutions to the risks.
Analyze project risks
A project's overall strategy should include a risk-management plan. Risk analysis helps you identify which parts of your project are most at risk. By identifying potential risks, a project manager can determine what measures to take to mitigate them. A solid risk management plan will outline the steps needed to minimize possible risks and minimize their effects. In this article, we'll discuss the different steps involved in risk management and discuss how to effectively analyze project risks.
Create a plan to minimize them
It is crucial to have a sound risk management plan in place. This plan will identify and prioritize risks for your business and help you minimize the negative impact of these risks. This responsibility cannot be left to just one person. Employees must be educated about risks and trained on mitigation strategies. Your risk mitigation strategy can only be as effective and efficient as the people you have and the resources available to them. By using a risk management system, you can keep your business running smoothly.
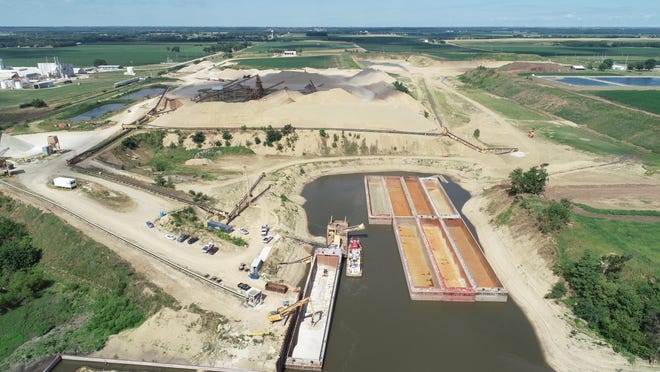
Archive your plan
Some organisations require that you archive your risk management plan. Some risk management plans may not work for all projects. In other cases, a risk management plan from a previous project can provide a foundation for future projects. Although it may not be necessary to archive your risk management plan, it is a good idea. Here are some tips to help you archive your plan. We hope that these tips will be of use to you.
FAQ
What are the four major functions of Management?
Management is responsible for organizing, managing, directing and controlling people, resources, and other activities. Management also involves setting goals and developing policies.
Management assists an organization in achieving its goals by providing direction, coordination and control, leadership, motivation, supervision and training, as well as evaluation.
Management has four primary functions:
Planning - Planning involves determining what needs to be done.
Organizing – Organizing means deciding how to organize things.
Direction - This is the art of getting people to follow your instructions.
Controlling - Controlling means ensuring that people carry out tasks according to plan.
What is a fundamental management tool for decision-making?
A decision matrix is an easy but powerful tool to aid managers in making informed decisions. It helps them think systematically about all the options available to them.
A decision matrix represents alternatives in rows and columns. It is easy to see how each option affects the other options.
In this example, there are four possible options represented by boxes on the left-hand side of the matrix. Each box represents a different option. The top row shows the status quo (the current situation), and the bottom row shows what would happen if nothing was done at all.
The middle column shows the effect of choosing Option 1. This would result in an increase of sales of $2 million to $3million.
These are the results of selecting Options 2 or 3. These are good changes, they increase sales by $1million or $500,000. These positive changes have their downsides. Option 2 increases costs by $100 thousand, while Option 3 decreases profits to $200 thousand.
The last column shows you the results of Option 4. This results in a decrease of sales by $1,000,000
The best thing about a decision matrix is the fact that you don't have to remember which numbers go with what. The best thing about a decision matrix is that you can simply look at the cells, and immediately know whether one option is better or not.
This is because your matrix has already done the hard work. It is as simple a matter of comparing all the numbers in each cell.
Here is an example of how a decision matrix might be used in your business.
Advertising is a decision that you make. If you do this, you will be able to increase revenue by $5000 per month. However, additional expenses of $10 000 per month will be incurred.
You can calculate the net result of investing in advertising by looking at the cell directly below the one that says "Advertising." That number is $15 thousand. Advertising is worth much more than the investment cost.
Which kind of people use Six Sigma
Six Sigma is well-known to those who have worked in operations research and statistics. However, anyone involved in any aspect of business can benefit from using it.
It requires high levels of commitment and leadership skills to be successful.
What is the difference of a program and project?
A program is permanent while a project can be temporary.
Projects usually have a goal and a deadline.
It is often done in a team that reports to another.
A program is usually defined by a set or goals.
It is often done by one person.
What is Six Sigma?
Six Sigma uses statistical analyses to locate problems, measure them, analyze root cause, fix problems and learn from the experience.
The first step to solving the problem is to identify it.
Next, data are collected and analyzed in order to identify patterns and trends.
The problem is then rectified.
The data are then reanalyzed to see if the problem is solved.
This continues until the problem has been solved.
What are the 3 main management styles?
The three major management styles are authoritarian (left-faire), participative and laissez -faire. Each style is unique and has its strengths as well as weaknesses. Which style do you prefer? Why?
Authoritarian – The leader sets a direction and expects everyone follows it. This style works best in large organizations that are stable and well-organized.
Laissez-faire: The leader lets each person decide for themselves. This style is most effective when the organization's size and dynamics are small.
Participative - Leaders listen to all ideas and suggestions. This style works best in smaller organizations where everyone feels valued.
Statistics
- 100% of the courses are offered online, and no campus visits are required — a big time-saver for you. (online.uc.edu)
- UpCounsel accepts only the top 5 percent of lawyers on its site. (upcounsel.com)
- As of 2020, personal bankers or tellers make an average of $32,620 per year, according to the BLS. (wgu.edu)
- This field is expected to grow about 7% by 2028, a bit faster than the national average for job growth. (wgu.edu)
- Our program is 100% engineered for your success. (online.uc.edu)
External Links
How To
How does Lean Manufacturing work?
Lean Manufacturing processes are used to reduce waste and improve efficiency through structured methods. They were developed in Japan by Toyota Motor Corporation (in the 1980s). The aim was to produce better quality products at lower costs. Lean manufacturing seeks to eliminate unnecessary steps and activities in the production process. It has five components: continuous improvement and pull systems; just-in time; continuous change; and kaizen (continuous innovation). It is a system that produces only the product the customer requests without additional work. Continuous improvement is constantly improving upon existing processes. Just-in-time refers to when components and materials are delivered directly to the point where they are needed. Kaizen is continuous improvement. This can be achieved by making small, incremental changes every day. Finally, 5S stands for sort, set in order, shine, standardize, and sustain. These five elements are used together to ensure the best possible results.
Lean Production System
Six key concepts are the basis of lean production:
-
Flow - focuses on moving information and materials as close to customers as possible.
-
Value stream mapping- This allows you to break down each step of a process and create a flowchart detailing the entire process.
-
Five S's – Sort, Put In Order Shine, Standardize and Sustain
-
Kanban - visual cues such as stickers or colored tape can be used to track inventory.
-
Theory of constraints - identify bottlenecks during the process and eliminate them with lean tools like Kanban boards.
-
Just-in-time - deliver components and materials directly to the point of use;
-
Continuous improvement is making incremental improvements to your process, rather than trying to overhaul it all at once.