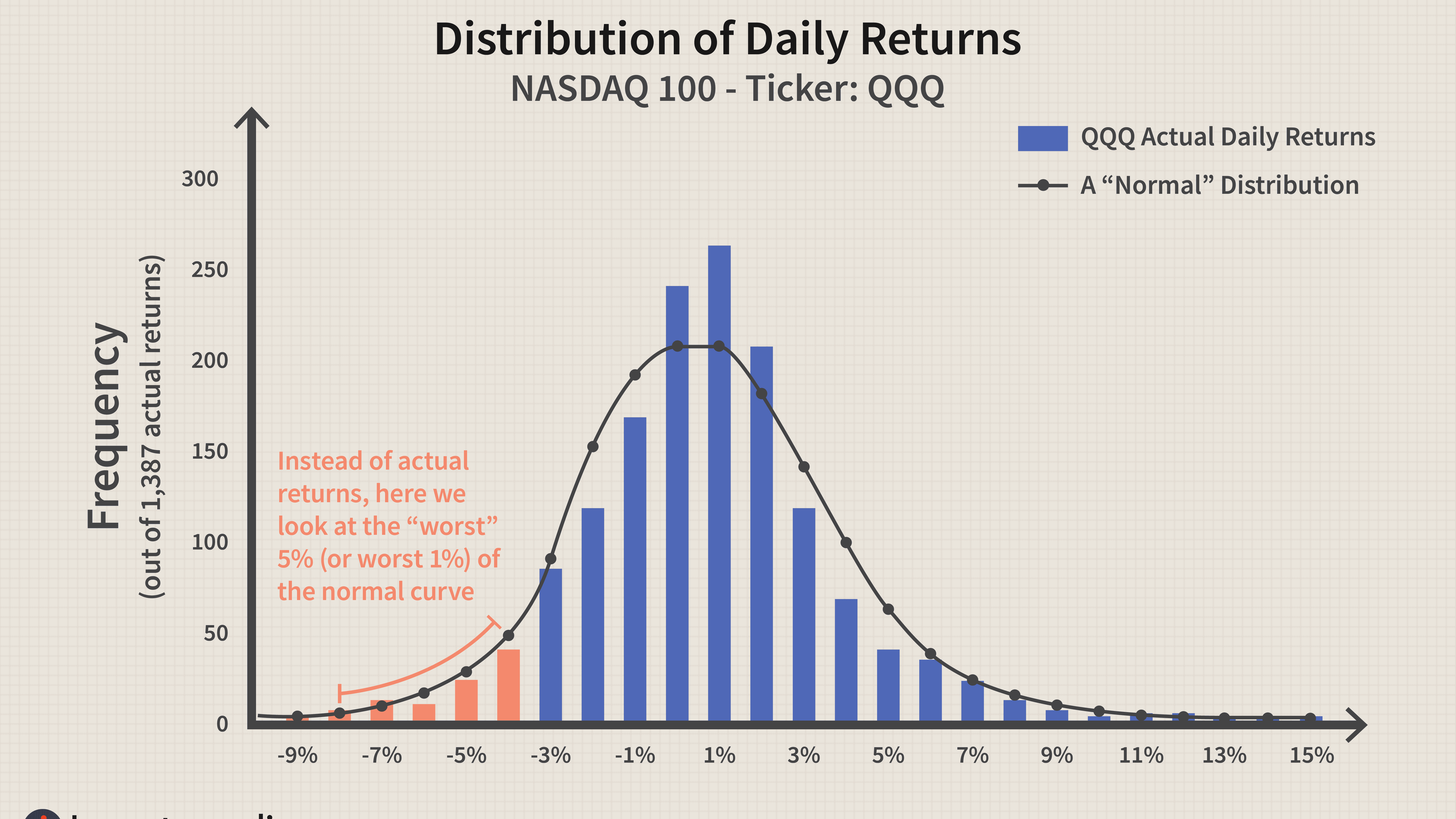
The Eisenhower matrix helps you manage your time more efficiently. The matrix will help you to identify the most worthwhile 20 percent. These tasks can then be given your attention. Eisenhower's method of managing your everyday life is powerful and tried-and-true. Using this method will help you prioritize and achieve long-term goals. To learn more, read this article. This article contains information on how to use the Eisenhower matrix.
Eisenhower's "urgent-important matrix"
The Eisenhower Matrix helps you prioritize tasks based on urgency and importance. Dwight D. Eisenhower (ex-US President) developed the Eisenhower Matrix. It's an important and effective tool for time management, project planning, and other organizational activities. You can also use it as a tool to make decisions. It's a decision-making framework with four squares - Urgent, Important, Critical, and Non-Critical.
The Eisenhower Matrix makes it easy to prioritize work and distinguish between important and urgent tasks. This will help you decide which tasks should be completed immediately and which should be delegated. Urgent tasks need immediate attention. Failure to complete them will result in severe consequences. Stress and burnout can be caused by delaying urgent tasks. It is important to understand the importance of each task so that you can prioritize them and avoid wasting time and resources.
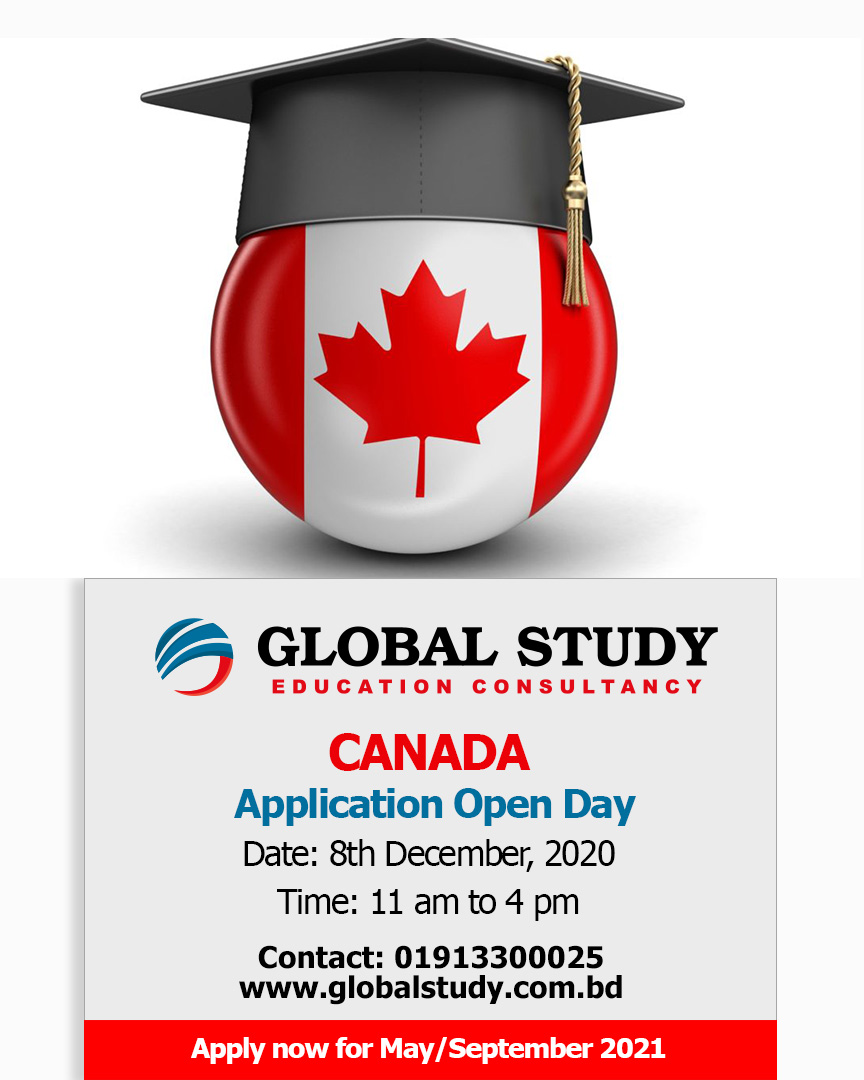
Structure of the EISENHOFER matrix
The Eisenhower Matrix is a time management tool designed by President Dwight D. Eisenhower. It was used by President Dwight D. Eisenhower to help him prioritize the most important matters. Stephen Covey made it popular in his 7 Habits of Highly Effective People. Now, it's used in many time-management and decision-making systems in companies and organizations. This time management tool will help you reach your goals.
The Eisenhower matrix emphasizes the importance of identifying tasks and their completion. Important tasks are tasks that directly contribute to the project's main goal. Urgent tasks require immediate action and can have a significant impact on other people. Each box represents one task. This will allow you to identify your most critical and urgent tasks. You can identify which tasks are most urgent by using an Eisenhower matrix. An Eisenhower matrix will allow you to view the priority of tasks each day and determine which tasks are most likely to interfere with your monthly target.
Identifying the most impactful 20 percent of your tasks
If you take a look at how many tasks you accomplish in a single day, you will see that only a very small number are actually impactful. These tasks are the ones you can dedicate most time to and get the greatest results from. You should circle the most significant tasks to make a list. These might include meeting with your leadership group, mentoring an employee, or strategic planning. These tasks are different from the daily tasks such as answering the phones or paying the bills. You should assign these top tasks to someone who can handle them well. As with all assignments, make sure they are held accountable for completing the job.
Maximizing productivity is possible by identifying the most important 20 percent. This rule is based in the Pareto principle. The principle states that only 20% percent of work produces 80% of results. This principle will help you prioritise your tasks, set realistic deadlines and increase your focus. Jolene is a medical coder working from home and uses the 80/20 principle to identify which tasks are important. These tasks take up seventy percent her day.
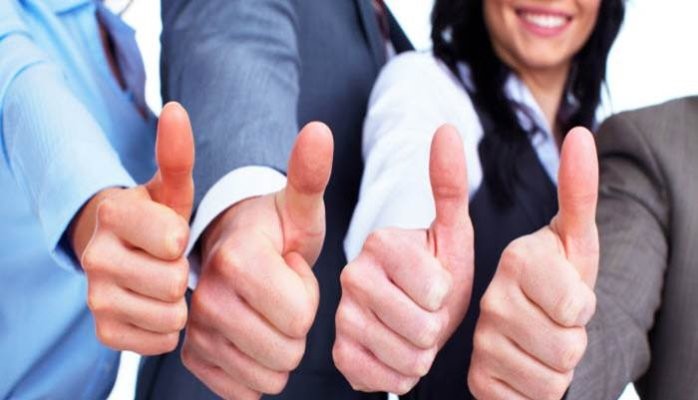
Managing your time using eisenhower matrix
The Eisenhower Matrix is a useful tool for time management. The Eisenhower Matrix is a time management tool that President Dwight D. Eisenhower created. Eisenhower was the 34th president of the United States and served two terms. He was an effective leader and one of only five Americans to earn the rank in Five-Star General. DARPA, also known as the Defence Advanced Research Projects Agency or DARPA was created by him. It eventually led to development of the Internet.
First, create a list with tasks that are color-coded to create an Eisenhower Matrix. Green tasks are called "do", while yellow tasks are called "schedule". Make a list with ten items for each quadrant. Include any important or urgent ones. To prioritize tasks, use a color-coded system and delegate or assign them to others.
FAQ
It can sometimes seem difficult to make business decisions.
Complex systems are often complex and have many moving parts. The people who run them must juggle multiple priorities at once while also dealing with uncertainty and complexity.
Understanding the impact of these factors on the system is crucial to making sound decisions.
It is important to consider the functions and reasons for each part of the system. It is important to then consider how the individual pieces relate to each other.
You should also ask yourself if there are any hidden assumptions behind how you've been doing things. If you don't have any, it may be time to revisit them.
Try asking for help from another person if you're still stuck. They might have different perspectives than you, and could offer insight that could help you solve your problem.
What role should a manager play within a company
Different industries have different roles for managers.
In general, a manager controls the day-to-day operations of a company.
He/she ensures that the company meets its financial obligations and produces goods or services that customers want.
He/she is responsible for ensuring that employees comply with all regulations and follow quality standards.
He/she is responsible for the development of new products and services, as well as overseeing marketing campaigns.
What's the difference between Six Sigma and TQM?
The major difference between the two tools for quality management is that six Sigma focuses on eliminating defect while total quality control (TQM), on improving processes and decreasing costs.
Six Sigma can be described as a strategy for continuous improvement. It emphasizes the elimination or minimization of defects through statistical methods such control charts and p charts.
This method has the goal to reduce variation of product output. This is done by identifying root causes and rectifying them.
Total Quality Management involves monitoring and measuring every aspect of the organization. It also includes the training of employees to improve performance.
It is often used to increase productivity.
What are management concepts?
Management concepts are the fundamental principles and practices that managers use when managing people and their resources. They include such topics as human resource policies, job descriptions, performance evaluations, training programs, employee motivation, compensation systems, organizational structure, and many others.
What is Kaizen and how can it help you?
Kaizen is a Japanese term meaning "continuous improvement." It is a philosophy that encourages employees to constantly look for ways to improve their work environment.
Kaizen is based on the belief that every person should be able to do his or her job well.
What are the steps in the decision-making process in management?
The decision-making process of managers is complicated and multifaceted. This involves many factors including analysis, strategy and planning, implementation, measurement and evaluation, feedback, feedback, and others.
It is important to remember that people are human beings, just like you. They make mistakes. There is always room to improve, especially if your first priority is to yourself.
This video explains the process of decision-making in Management. We'll discuss the different types and reasons they are important. Managers should also know how to navigate them. Here are some topics you'll be learning about:
How to manage employees effectively?
Effectively managing employees means making sure they are productive and happy.
It means setting clear expectations for them and keeping an eye on their performance.
Managers need clear goals to be able to accomplish this.
They should communicate clearly to staff members. They should also ensure that they both reward high performers and discipline those who are not performing to their standards.
They must also keep records of team activities. These include:
-
What did we accomplish?
-
How much work was put in?
-
Who did it all?
-
What was the moment it was completed?
-
Why it was done?
This data can be used to evaluate and monitor performance.
Statistics
- This field is expected to grow about 7% by 2028, a bit faster than the national average for job growth. (wgu.edu)
- UpCounsel accepts only the top 5 percent of lawyers on its site. (upcounsel.com)
- As of 2020, personal bankers or tellers make an average of $32,620 per year, according to the BLS. (wgu.edu)
- The profession is expected to grow 7% by 2028, a bit faster than the national average. (wgu.edu)
- Your choice in Step 5 may very likely be the same or similar to the alternative you placed at the top of your list at the end of Step 4. (umassd.edu)
External Links
How To
What is Lean Manufacturing?
Lean Manufacturing techniques are used to reduce waste while increasing efficiency by using structured methods. They were created in Japan by Toyota Motor Corporation during the 1980s. The goal was to produce quality products at lower cost. Lean manufacturing seeks to eliminate unnecessary steps and activities in the production process. It has five components: continuous improvement and pull systems; just-in time; continuous change; and kaizen (continuous innovation). Pull systems are able to produce exactly what the customer requires without extra work. Continuous improvement is the continuous improvement of existing processes. Just-in time refers to components and materials being delivered right at the place they are needed. Kaizen means continuous improvement. Kaizen involves making small changes and improving continuously. Last but not least, 5S is for sort. These five elements work together to produce the best results.
Lean Production System
Six key concepts form the foundation of the lean production system:
-
Flow - focus on moving material and information as close to customers as possible;
-
Value stream mapping- This allows you to break down each step of a process and create a flowchart detailing the entire process.
-
Five S’s - Sorted, In Order. Shine. Standardize. And Sustain.
-
Kanban is a visual system that uses visual cues like stickers, colored tape or stickers to keep track and monitor inventory.
-
Theory of Constraints - Identify bottlenecks in the process, and eliminate them using lean tools such kanban boards.
-
Just-intime - Order components and materials at your location right on the spot.
-
Continuous improvement - Make incremental improvements rather than overhauling the entire process.