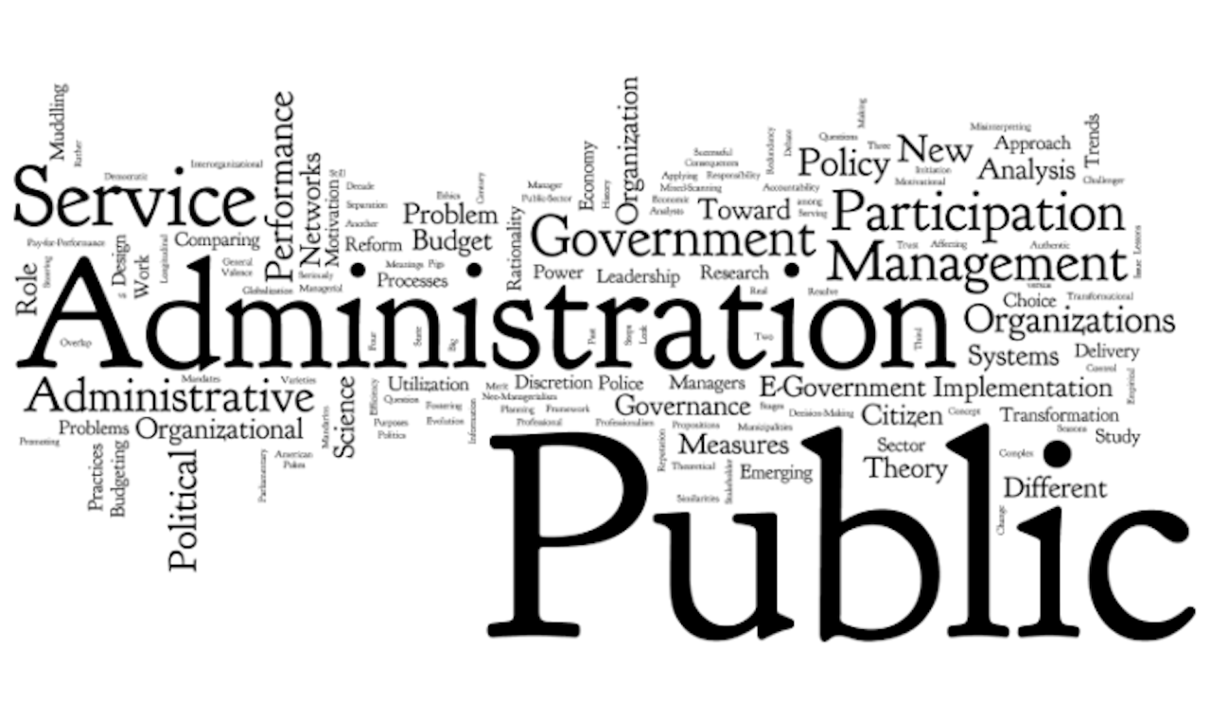
Supply chain success is based on five elements. These elements include collaboration, cost reduction, managing upstream and downstream business issues, and working with suppliers. Identifying and implementing each of these elements is vital for supply chain success. In addition, there are some government and regulatory bodies that influence supply chain success.
Five strategy elements for supply chain success
Supply chain management plays a critical role in any organization's success, especially if you wish to satisfy customer expectations. This is why your supply chain strategy must focus on customer needs. This means that your fulfillment experience must be consistent with what the brand promises. If a brand promises quick delivery, it must be capable of fulfilling that promise. Customers also appreciate the small things. Customers also appreciate thoughtfulness. This is an indication of the thought process behind the brand.
Supplier issues are a key part of a successful supply chain strategy. Delays can also be caused by suppliers having to pay tariffs. These delays can be avoided by finding alternative suppliers or buying bulk before tariffs go into effect. These delays can be overcome by a supply chain solution. Such software can provide precise information about inventory movements and inventory levels.
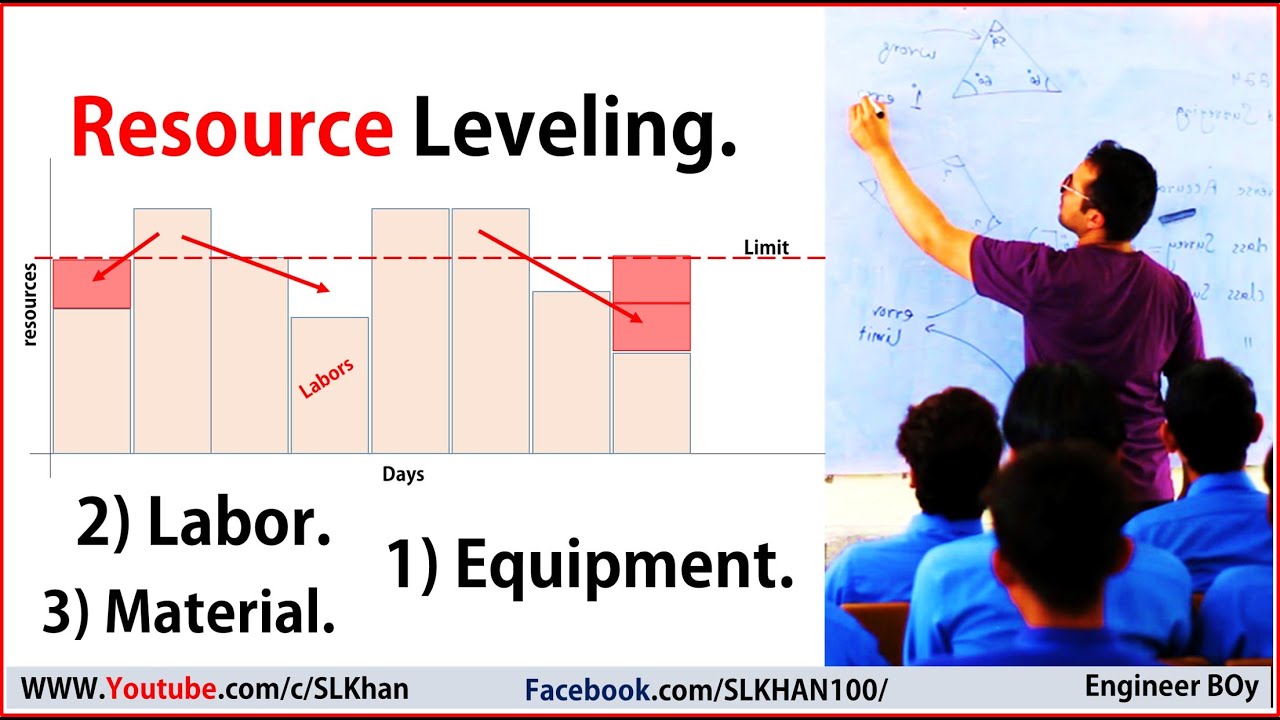
Success in supply chains is determined by the actions of government agencies and regulators
Supply chain success is affected by many factors, including government policies. The United States government spends federal dollars promoting domestic capacity and developing markets abroad, while simultaneously promoting collaborative mechanisms between foreign countries and domestic companies. These mechanisms can be public, private, or cross-government. These efforts are designed to help companies meet their dual objectives, which depend on a global supply chain that is trusted and robust.
This is particularly important in the healthcare industry as it can have a significant impact on the supply of healthcare products. Hospitals may have to stock the correct sizes of gloves while patients may require specific medical products. Financial managers may wish to reduce the number of out-of-date medical products and decrease healthcare costs. Other financial professionals may prefer specific types or brands of medical products. A lack of coordination can lead to disruptions in supply chains.
Collaboration with suppliers
Supply chain collaboration involves working with suppliers to increase the efficiency of a company’s procurement of goods or services. It has a number of benefits for both companies. Collaboration is more flexible than traditional customer-supplier relationships and focuses on creating mutual value. In addition, collaboration allows companies to view their suppliers as strategic partners with whom they can work to gain competitive advantage.
A supply chain's success is dependent on the collaboration of suppliers. Each party must find ways to improve the relationship between them in order to maximize collaboration's value. You can do this by holding regular meetings between you and your suppliers. You can discuss your concerns with them and give constructive feedback.

Problems relating to upstream or downstream businesses
Supply chain management is the integration of many processes and tasks with an emphasis on delivering value for customers and other stakeholders. There are many issues involved, including operational, reputational and legal risks. Because they can directly impact the success of a supply network, it is vital to manage these issues.
It is essential that supply chain managers understand the main issues affecting their business and can develop solid management plans. Additionally, they must establish strong contracts with their suppliers and cooperate with their customers to address potential issues. It is essential that supply chain managers are proactive in dealing with global economic instability and increasing complexity. The introduction of tariffs to trade routes may lead to higher costs and slower customs processing times.
FAQ
Why does it sometimes seem so difficult to make good business decisions?
Complex systems with many moving parts are the hallmark of businesses. It is difficult for people in charge of businesses to manage multiple priorities simultaneously and also deal with uncertainty.
It is important to understand the effects of these factors on the system in order to make informed decisions.
You must first consider what each piece of the system does and why. You then need to consider how those individual pieces interact with each other.
Also, you should ask yourself if there have been any assumptions in your past behavior. If not, you might want to revisit them.
For help, ask someone else if you're still stumped after all the above. You might find their perspective is different from yours and they may have insight that can help you find the solution.
How do we build a culture that is successful in our company?
A culture of respect and value within a company is key to a productive culture.
It is founded on three basic principles:
-
Everyone has something to contribute
-
Fair treatment of people is the goal
-
It is possible to have mutual respect between groups and individuals
These values reflect in how people behave. For example, they will treat others with courtesy and consideration.
They will be respectful of the opinions of other people.
They can also be a source of inspiration for others.
A company culture encourages collaboration and communication.
People feel free to express their views openly without fear of reprisal.
They understand that errors will be tolerated as long they are corrected honestly.
Finally, the company culture encourages honesty as well as integrity.
Everyone understands that the truth is always best.
Everyone is aware that rules and regulations apply to them.
No one is entitled to any special treatment or favors.
What's the difference between leadership & management?
Leadership is about influence. Management is about controlling others.
Leaders inspire others, managers direct them.
A leader motivates people and keeps them on task.
A leader develops people; a manager manages people.
What are the 3 basic management styles?
The three basic management styles are: authoritarian, laissez-faire, and participative. Each style has its strengths and weaknesses. What style do you prefer? Why?
Authoritarian – The leader sets a direction and expects everyone follows it. This style works best in large organizations that are stable and well-organized.
Laissez-faire – The leader gives each individual the freedom to make decisions for themselves. This style is best when the organization has a small but dynamic group.
Participative: The leader listens to everyone's ideas and suggestions. This style is best for small organizations where everyone feels valued.
How does Six Sigma work
Six Sigma uses statistical analysis for problems to be found, measured, analyzed root causes, corrected, and learned from.
The first step to solving the problem is to identify it.
The data is then analyzed and collected to identify trends.
Then, corrective actions can be taken to resolve the problem.
Finally, data will be reanalyzed to determine if there is an issue.
This cycle continues until there is a solution.
What are the five management processes?
Planning, execution, monitoring and review are the five stages of any business.
Setting goals for the future requires planning. Planning includes setting goals for the future.
Execution is the actual execution of the plans. Everyone involved must follow them.
Monitoring is checking on progress towards achieving your objectives. This should involve regular reviews of performance against targets and budgets.
Each year, reviews are held at the end. They provide an opportunity to assess whether everything went well during the year. If not, changes may be made to improve the performance next time around.
After the annual review is complete, evaluations are conducted. It helps to identify what went well and what didn’t. It also provides feedback regarding how people performed.
Statistics
- The BLS says that financial services jobs like banking are expected to grow 4% by 2030, about as fast as the national average. (wgu.edu)
- This field is expected to grow about 7% by 2028, a bit faster than the national average for job growth. (wgu.edu)
- As of 2020, personal bankers or tellers make an average of $32,620 per year, according to the BLS. (wgu.edu)
- Your choice in Step 5 may very likely be the same or similar to the alternative you placed at the top of your list at the end of Step 4. (umassd.edu)
- 100% of the courses are offered online, and no campus visits are required — a big time-saver for you. (online.uc.edu)
External Links
How To
How can you implement the Kaizen technique?
Kaizen means continuous improvement. The term was coined in the 1950s at Toyota Motor Corporation and refers to the Japanese philosophy emphasizing constant improvement through small incremental changes. It's a process where people work together to improve their processes continuously.
Kaizen is one of the most effective methods used in Lean Manufacturing. The concept involves employees responsible for manufacturing identifying problems and trying to fix them before they become serious issues. This increases the quality of products and reduces the cost.
Kaizen is a way to raise awareness about what's happening around you. So that there is no problem, you should immediately correct it if something goes wrong. Report any problem you see at work to your manager.
Kaizen is based on a few principles. Always start with the end product in mind and work our way back to the beginning. For example, if we want to improve our factory, we first fix the machines that produce the final product. Next, we repair the machines that make components. Then, the machines that make raw materials. Then we fix the workers, who directly work with these machines.
This approach is called 'kaizen' because it focuses on improving everything steps by step. Once the factory is fixed, we return to the original site and work our way back until we get there.
To implement kaizen in your business, you need to find out how to measure its effectiveness. There are many ways to tell if kaizen is effective. Another way to determine if kaizen is working well is to look at the quality of the products. Another method is to determine how much productivity has improved since the implementation of kaizen.
A good way to determine whether kaizen has been implemented is to ask why. Did you do it because it was legal or to save money? Did you really believe that it would be a success factor?
Let's say you answered yes or all of these questions. Congratulations! You are now ready to begin kaizen.