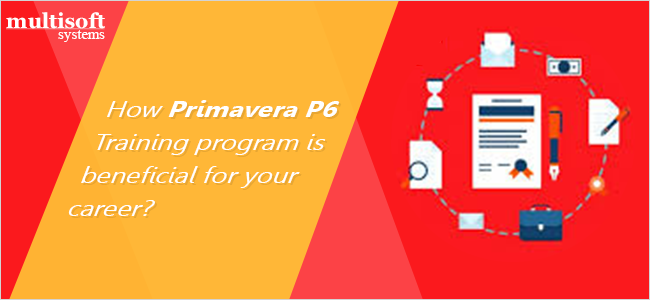
Time blocking helps you manage your time more efficiently by helping you to decide which tasks are urgent and which can wait. This method reduces the amount of time you spend on unimportant tasks and helps you feel more productive. This method can help you reach larger goals quicker. If you don't have the time or patience to complete all your tasks, this is the best time management strategy.
Time blocking is an effective time management strategy
Time blocking is a way to block time for specific tasks. This will ensure that you complete important tasks and not waste your time on lower-priority tasks. It is a great method to get back your time. Many people underestimate the time it takes to accomplish important tasks. This strategy allows you to visualise your time blocks. It can also help you avoid interruptions.
Time blocking does not always work for everyone. For example, it's not feasible for people with reactive jobs, who must constantly prioritise tasks to meet customer demands. This strategy will not work if you have to deal with unexpected tasks or last-minute meeting requests. In this case, you might need to change some of the time that you have scheduled to be flexible, such as the afternoon.
It reduces procrastination
Time blocking is helpful when it comes down to work and family. It is possible to make sure that both personal and professional tasks are included in your daily schedule by creating a daily list. You can also plan time to spend with your family and friends. Even if you must miss a family event you can use time blocking to fit them in.
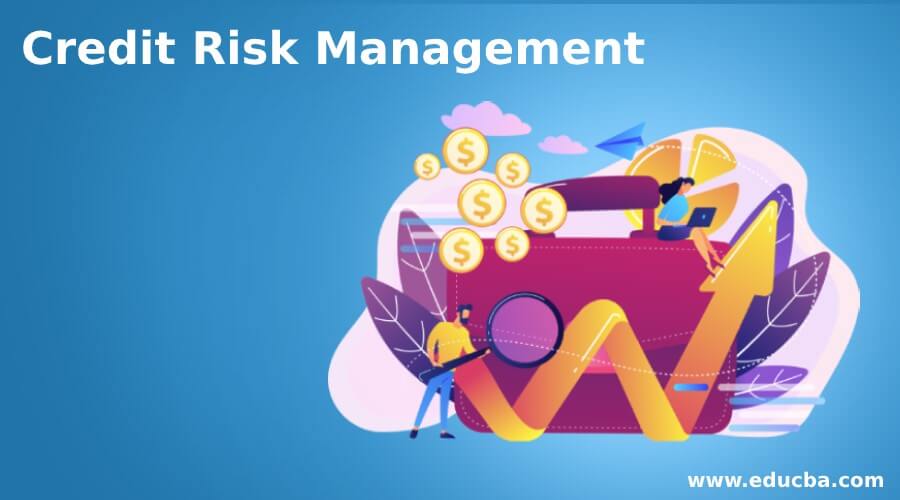
Procrastination can be reduced by scheduling tasks and activities. Task batching allows you to group related tasks. For example, scheduling two 20-minute blocks of email processing can be more effective than checking email every 15 minutes.
It improves productivity
Time blocking can be a time management strategy that increases productivity. This method allows you to plan your time so that you can complete your tasks at the best time possible. It's also a great method to save time and allow you to grow personally, by taking online courses or learning new skills.
The most common mistake people make with time blocking is to make their time slots too small. This can lead overconfidence which makes it hard to let go of some tasks. It is possible to increase the size and duration of your time slots.
It improves mental wellbeing
Time blocking can be used to prioritize tasks and assign time to the correct ones. It helps people to focus on one specific task at a time, rather than procrastinating or doing other things that are more important in the moment. To avoid procrastination, creating a time-block is a great idea. It can help you to have a clear mind, reduce your workload and take on more responsibilities. Procrastination is also known to increase stress levels and negatively impact memory.
Many people find it hard to break down big tasks into smaller ones. People also struggle with work-life balance and finding time to have fun. This can be a serious issue, so it's worth trying out a new way to work. You can accomplish more, achieve deeper goals, and be more efficient. These benefits last a lifetime and are not short-term.
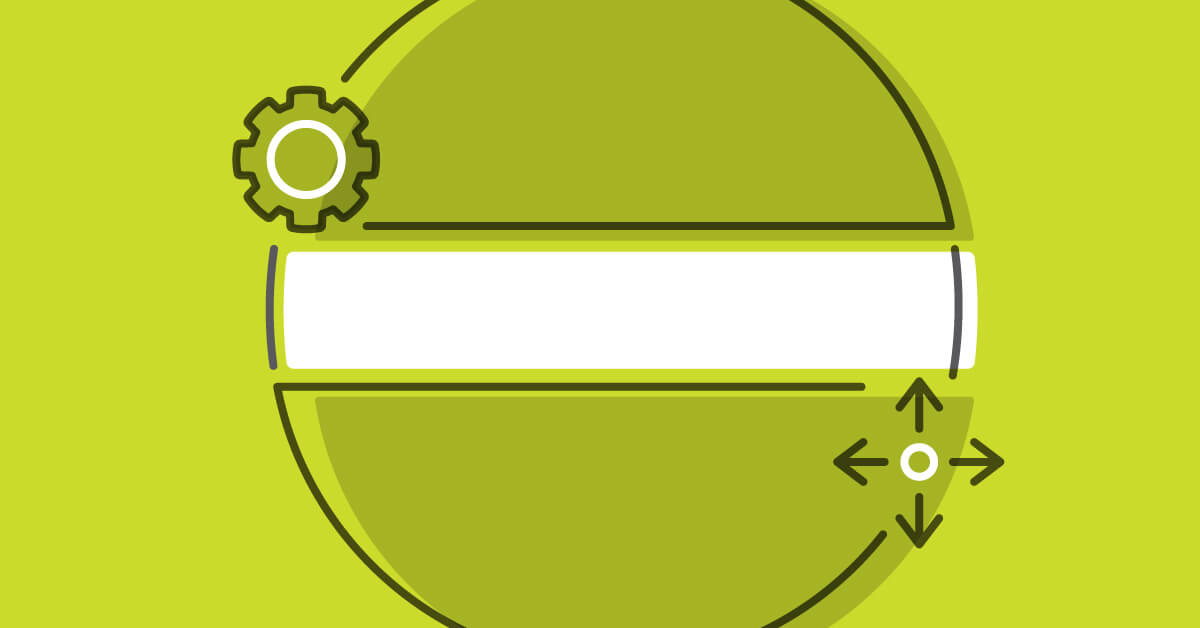
It helps to reduce context switching
Time blocking is an effective method to increase focus, and reduce context switching. It allows you to focus on one task at a time and avoid distractions. But it is important that you allow some space for more complex tasks. The less you worry about distractions, the smaller your time block.
Context switching can affect your productivity and happiness. Whenever you are working on more than one task at the same time, you are wasting valuable time. You may even feel tired. Juggling several tasks can take up to 17% of your time, according to estimates.
FAQ
What is the difference in leadership and management?
Leadership is about being a leader. Management is about controlling others.
A leader inspires followers while a manager directs workers.
A leader inspires others to succeed, while a manager helps workers stay on task.
A leader develops people; a manager manages people.
What are the most common errors made by managers?
Sometimes, managers make their job more difficult than it is.
They may not delegate enough responsibilities and not provide sufficient support.
Managers often lack the communication skills necessary to motivate and guide their teams.
Managers set unrealistic expectations and make it difficult for their team.
Managers may choose to solve every problem all by themselves, instead of delegating to others.
How does Six Sigma work
Six Sigma uses statistical analyses to locate problems, measure them, analyze root cause, fix problems and learn from the experience.
The first step is identifying the problem.
The data is then analyzed and collected to identify trends.
Then corrective actions are taken to solve the problem.
The data are then reanalyzed to see if the problem is solved.
This cycle continues until the problem is solved.
What is a basic management tool used in decision-making?
The decision matrix is a powerful tool that managers can use to help them make decisions. They can think about all options and make informed decisions.
A decision matrix represents alternatives in rows and columns. It is easy to see how each option affects the other options.
In this example, we have four possible alternatives represented by the boxes on the left side of the matrix. Each box represents one option. The top row represents the current state of affairs, and the bottom row is indicative of what would happen in the event that nothing were done.
The middle column displays the impact of selecting Option 1. In this case, it would mean increasing sales from $2 million to $3 million.
The next two columns show the effects of choosing Options 2 and 3. These are both positive changes that increase sales by $1million and $500,000. These changes can also have negative effects. For instance, Option 2 increases cost by $100 thousand while Option 3 reduces profits by $200 thousand.
Finally, the last column shows the results of choosing Option 4. This would result in a reduction of sales of $1 million.
The best thing about a decision matrix is the fact that you don't have to remember which numbers go with what. You just look at the cells and know immediately whether any given a choice is better than another.
The matrix already does all the work. It's simply a matter of comparing the numbers in the relevant cells.
Here's an example showing how you might use a Decision Matrix in your business.
Decide whether you want to invest more in advertising. If you do, you'll be able to increase your revenue by $5 thousand per month. But, you will also incur additional expenses of $10 thousand per month.
If you look at the cell that says "Advertising", you can see the number $15,000. Therefore, you should choose to invest in advertising since it is worth more than the cost involved.
Why is project management so important?
Project management techniques ensure that projects run smoothly while meeting deadlines.
This is because most businesses rely on project work for their products and services.
These projects require companies to be efficient and effective managers.
Companies could lose their time, reputation, and money without effective project management.
What is TQM, exactly?
The industrial revolution was when companies realized that they couldn't compete on price alone. This is what sparked the quality movement. They had to improve efficiency and quality if they were to remain competitive.
Management responded to the need to improve, and developed Total Quality Management (TQM). This focused on improving every aspect of an organization’s performance. It involved continuous improvement, employee participation, and customer satisfaction.
Statistics
- As of 2020, personal bankers or tellers make an average of $32,620 per year, according to the BLS. (wgu.edu)
- This field is expected to grow about 7% by 2028, a bit faster than the national average for job growth. (wgu.edu)
- UpCounsel accepts only the top 5 percent of lawyers on its site. (upcounsel.com)
- Our program is 100% engineered for your success. (online.uc.edu)
- 100% of the courses are offered online, and no campus visits are required — a big time-saver for you. (online.uc.edu)
External Links
How To
How can Lean Manufacturing be done?
Lean Manufacturing processes are used to reduce waste and improve efficiency through structured methods. They were created in Japan by Toyota Motor Corporation during the 1980s. The primary goal was to make products with lower costs and maintain high quality. Lean manufacturing emphasizes removing unnecessary steps from the production process. It is composed of five fundamental elements: continuous improvement; pull systems, continuous improvements, just-in–time, kaizen, continuous change, and 5S. It is a system that produces only the product the customer requests without additional work. Continuous improvement is constantly improving upon existing processes. Just-intime refers the time components and materials arrive at the exact place where they are needed. Kaizen is continuous improvement. This can be achieved by making small, incremental changes every day. Fifth, the 5S stand for sort, set up in order to shine, standardize, maintain, and standardize. These five elements can be combined to achieve the best possible results.
Lean Production System
Six key concepts are the basis of lean production:
-
Flow: The goal is to move material and information as close as possible from customers.
-
Value stream mapping - break down each stage of a process into discrete tasks and create a flowchart of the entire process;
-
Five S's: Sort, Shine Standardize, Sustain, Set In Order, Shine and Shine
-
Kanban: Use visual signals such stickers, colored tape, or any other visual cues, to keep track your inventory.
-
Theory of constraints - identify bottlenecks in the process and eliminate them using lean tools like kanban boards;
-
Just-intime - Order components and materials at your location right on the spot.
-
Continuous improvement - Make incremental improvements rather than overhauling the entire process.