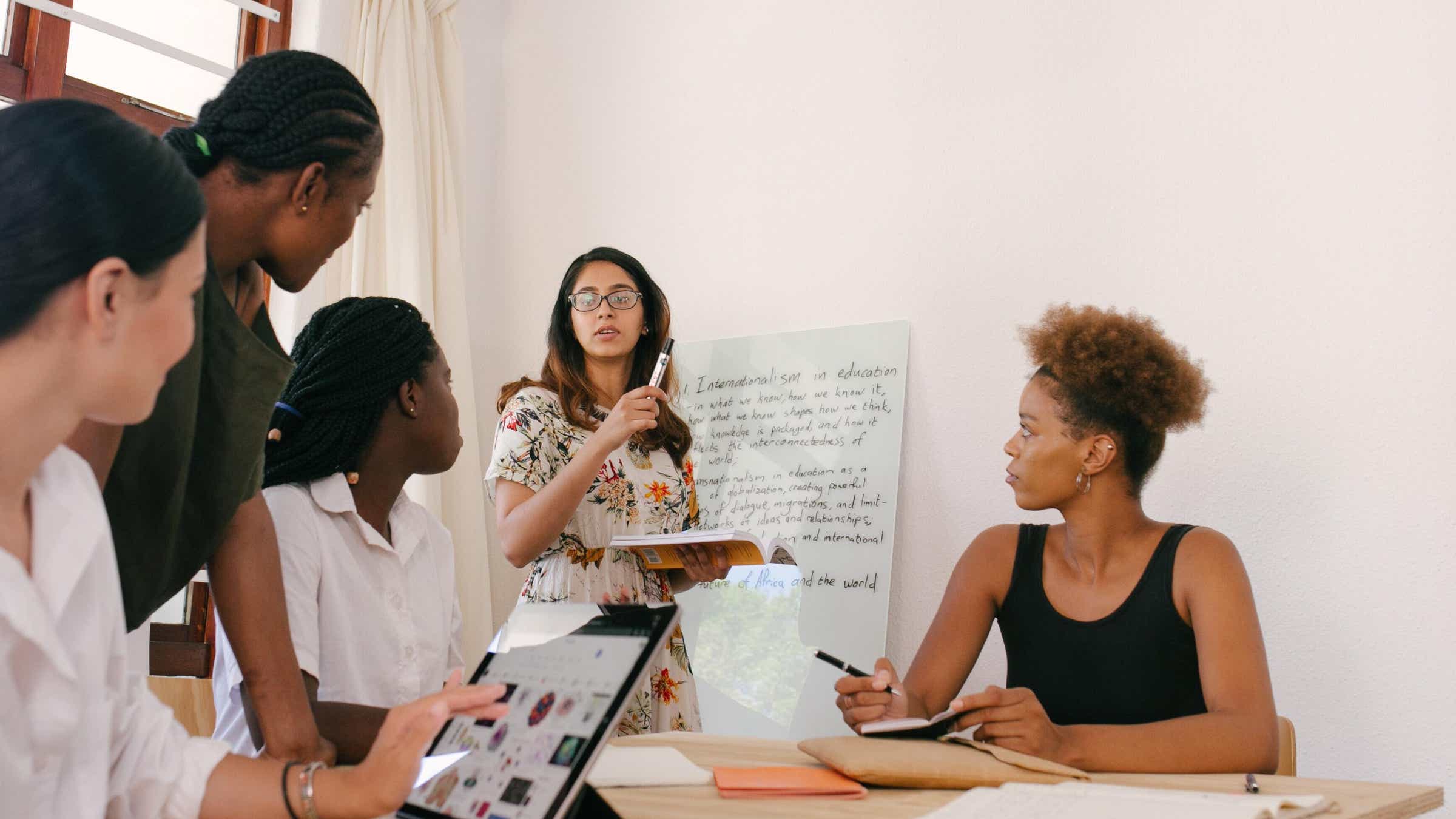
There are many styles of management. One type of management is top-down. Top-down leadership emphasizes hierarchy and punishing employees who fail to follow orders. This management style relies on intimidation or fear to keep employees on the right track. Other types emphasize the importance empathy. Both types can be equally successful. I'd be happy to answer any questions you might have about management. I would love to help you find the right job and answer your questions!
Principles of Management
The fundamental principle of management is to create a cause-and–effect relationship between actions and their outcomes. In other words, an effective management strategy will help you establish a link between your actions and the outcomes you desire. The principles of management are generally universal and apply to all types of organisations, no matter how large or small. The following article will discuss some of the most common principles and their application to different types of organisations. Keep reading to find out more.
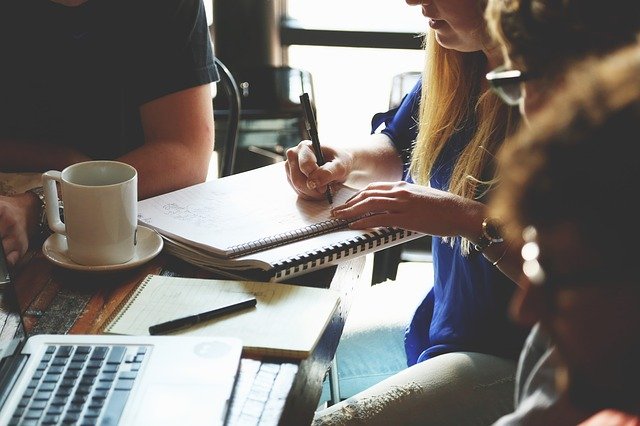
Management functions
Management consists of planning, organizing staff, leading and managing. Managers can devote different amounts to each of these functions depending on their organization's level. Additionally, organizing and planning are distinct from leading or controlling, which are both continuous processes. The organizing function includes defining a plan and allocating resources in the most efficient manner. The ultimate goal of management is to get to the destination without any difficulties.
Impact of technology on management
Technology has had a tremendous impact on business management. In the early 1900s, a French mining engineer, Henri Fayol, described a scientific method for managing a business. Fayol outlined six fundamental functions that managers should fulfill. These functions impact nearly every department in large companies. Computer hardware and software changed the way work was organized and directed. Although many managers are the same, they have seen a dramatic shift in the way they run their businesses.
Empathy in management is important
Many people think empathy is about feeling and connecting with others. However, there are many real-world benefits to empathy for organizations. Empathy is linked to organizational and social success. As people become more distant and less concerned about others' lives, empathy definitions have been rewritten. It can be difficult to feel empathy in such a context. This article will help you to cultivate empathy in your organization.
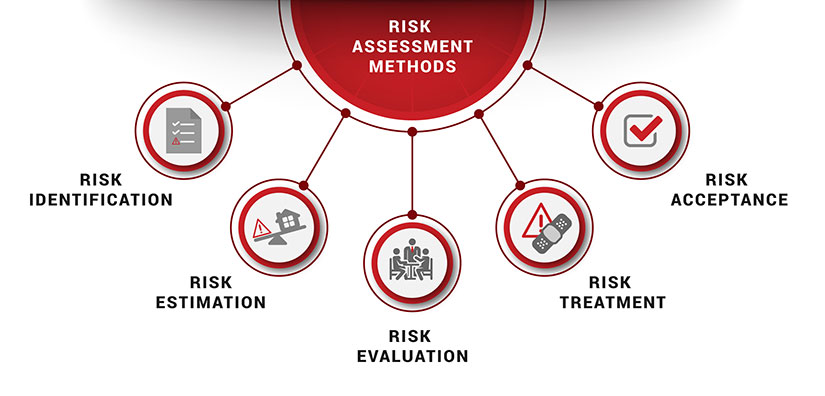
Bad management is costly
Management mistakes can result in lost productivity. Gallup estimates that a single disgruntled employee is worth $360 billion annually. Another cost is the disengagement of employees. The business suffers enormously in both of these cases. Poor management is not only a loss in productivity but it also has a negative impact on the bottom-line. Below are five signs that poor management is costing businesses money.
FAQ
What is a management tool to help with decision-making?
The decision matrix is a powerful tool that managers can use to help them make decisions. They can think about all options and make informed decisions.
A decision matrix is a way of representing alternatives as rows and columns. This allows you to easily see how each choice affects others.
In this example, we have four possible alternatives represented by the boxes on the left side of the matrix. Each box represents an option. The top row depicts the current status quo, while the bottom row represents what would happen if no action was taken.
The effect of Option 1 can be seen in the middle column. In this case, it would mean increasing sales from $2 million to $3 million.
The following columns illustrate the impact of Options 2 and 3. These positive changes can increase sales by $1 million or $500,000. However, these also involve negative consequences. Option 2 increases the cost of goods by $100,000. Option 3 decreases profits and makes them less attractive by $200,000.
The last column displays the results of selecting Option 4. This will result in sales falling by $1,000,000
A decision matrix has the advantage that you don’t have to remember where numbers belong. Simply look at the cells to instantly determine if one choice is better than the other.
This is because the matrix has done all the hard work. It's as easy as comparing numbers in the appropriate cells.
Here is an example of how a decision matrix might be used in your business.
Advertising is a decision that you make. This will allow you to increase your revenue by $5000 per month. However, additional expenses of $10 000 per month will be incurred.
The net result of advertising investment can be calculated by looking at the cell below that reads "Advertising." It is 15 thousand. Advertising is a worthwhile investment because it has a higher return than the costs.
What are some of the common mistakes made by managers?
Managers sometimes make their own job harder than necessary.
They may not be able to delegate enough responsibility to staff or provide adequate support.
Many managers lack the communication skills to motivate and lead their employees.
Managers set unrealistic expectations and make it difficult for their team.
Managers may choose to solve every problem all by themselves, instead of delegating to others.
What are the steps to take in order to make a management decision?
The decision-making process of managers is complicated and multifaceted. It involves many factors, such as analysis and strategy, planning, execution, measurement, evaluation, feedback etc.
It is important to remember that people are human beings, just like you. They make mistakes. You can always improve your performance, provided you are willing to make the effort.
In this video, we explain what the decision-making process looks like in Management. We'll discuss the different types and reasons they are important. Managers should also know how to navigate them. These topics are covered in this course:
What is the difference between TQM and Six Sigma?
The main difference in these two quality management tools lies in the fact that six sigma is focused on eliminating defects and total quality management (TQM), emphasizes improving processes and reducing costs.
Six Sigma is a methodology for continuous improvement. It emphasizes the elimination or minimization of defects through statistical methods such control charts and p charts.
This method attempts to reduce variations in product output. This is achieved by identifying and addressing the root causes of problems.
Total Quality Management involves monitoring and measuring every aspect of the organization. It also includes training employees to improve performance.
It is used to increase productivity.
Statistics
- This field is expected to grow about 7% by 2028, a bit faster than the national average for job growth. (wgu.edu)
- UpCounsel accepts only the top 5 percent of lawyers on its site. (upcounsel.com)
- 100% of the courses are offered online, and no campus visits are required — a big time-saver for you. (online.uc.edu)
- Your choice in Step 5 may very likely be the same or similar to the alternative you placed at the top of your list at the end of Step 4. (umassd.edu)
- Our program is 100% engineered for your success. (online.uc.edu)
External Links
How To
How can you use the Kaizen method?
Kaizen means continuous improvement. The Japanese philosophy emphasizes small, incremental improvements to achieve continuous improvement. This term was created by Toyota Motor Corporation in 1950. It's where people work together in order to improve their processes constantly.
Kaizen is one the most important methods of Lean Manufacturing. In this concept, employees who are responsible for the production line must identify problems that exist during the manufacturing process and try to solve them before they become big issues. This increases the quality of products and reduces the cost.
Kaizen is about making everyone aware of the world around them. Correct any errors immediately to avoid future problems. So, if someone notices a problem while working, he/she should report it to his/her manager.
When doing kaizen, there are some principles we must follow. When working with kaizen, we always start with the end result and move towards the beginning. If we want to improve our factory for example, we start by fixing the machines that make the final product. We then fix the machines producing components, and the machines producing raw materials. Finally, we repair the workers who are directly involved with these machines.
This is known as "kaizen", because it emphasizes improving each step. Once we have finished fixing the factory, we return to the beginning and work until perfection.
You need to know how to measure the effectiveness of kaizen within your business. There are several ways that you can tell if your kaizen system is working. One of these ways is to check the number of defects found on the finished products. Another way is to check how much productivity has grown since kaizen was implemented.
To determine if kaizen is effective, you should ask yourself why you chose to implement kaizen. Was it just because it was the law or because you wanted to save money? Did you really believe it would lead to success?
Let's say you answered yes or all of these questions. Congratulations! You are ready to start kaizen.